Empowering the Future of Robotics
QNX provides the robust and reliable software foundation necessary to drive innovation in the robotics industry. Our embedded solutions are trusted in a wide array of robotic applications, from industrial automation and logistics to advanced agricultural systems and autonomous mobile robots.
By delivering real-time performance, safety certifications, and unwavering security, QNX enables robotic manufacturers to create cutting-edge technology that enhances efficiency, safety, and productivity across diverse sectors. We are dedicated to providing the core software that allows our partners to build the next generation of intelligent, autonomous systems.
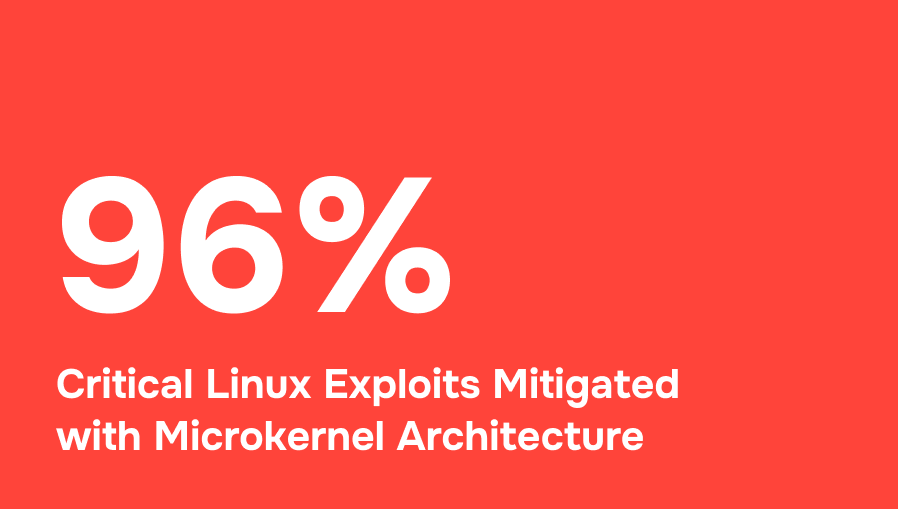
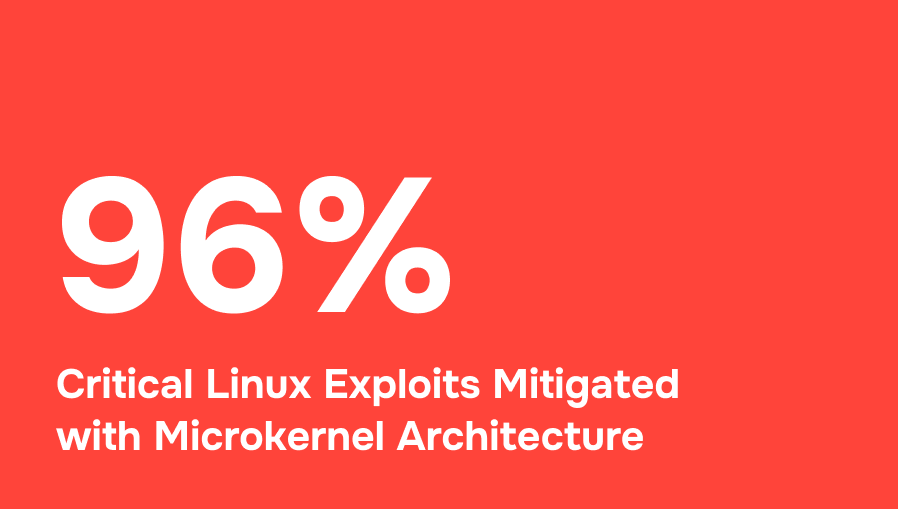
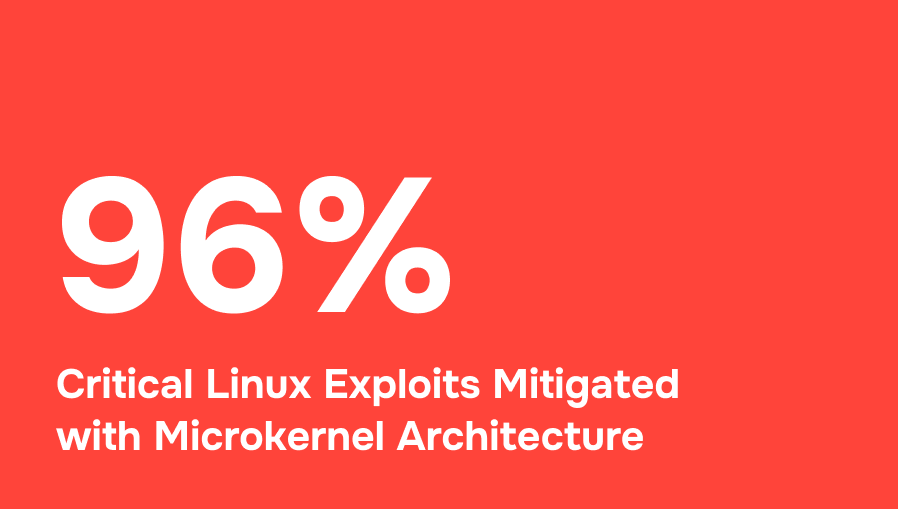
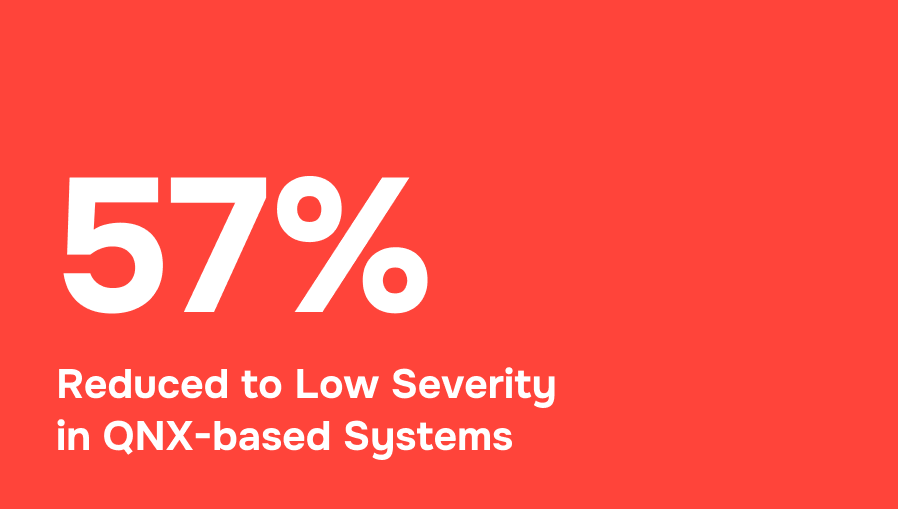
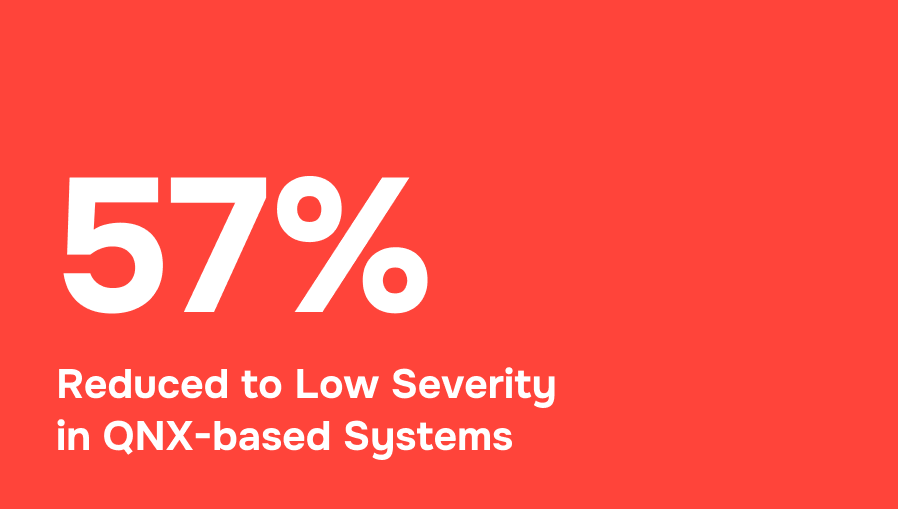
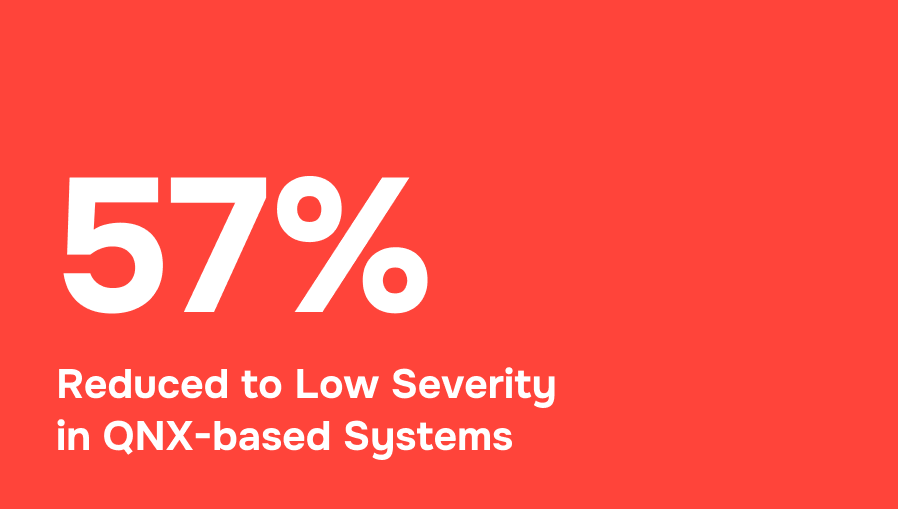
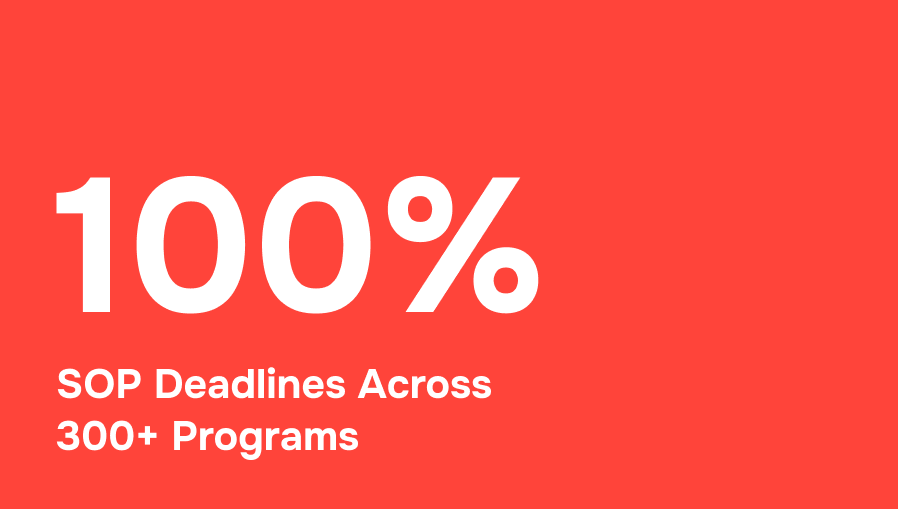
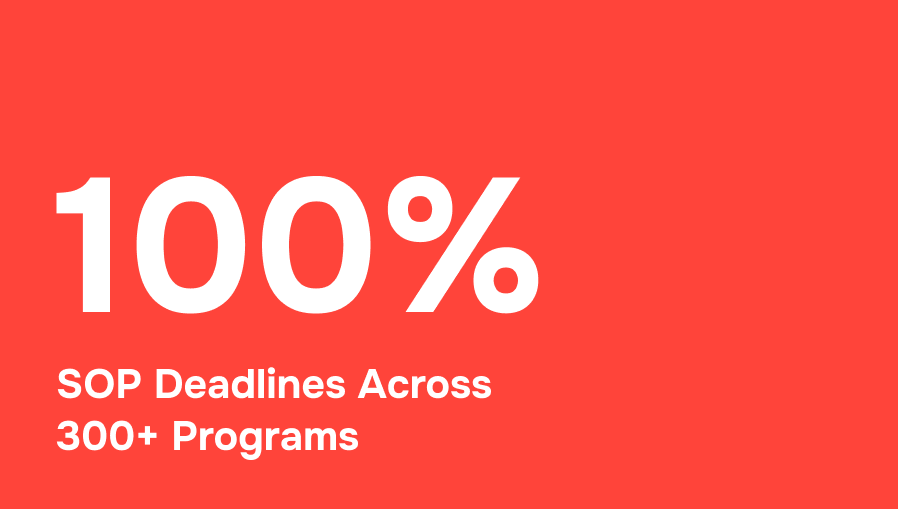
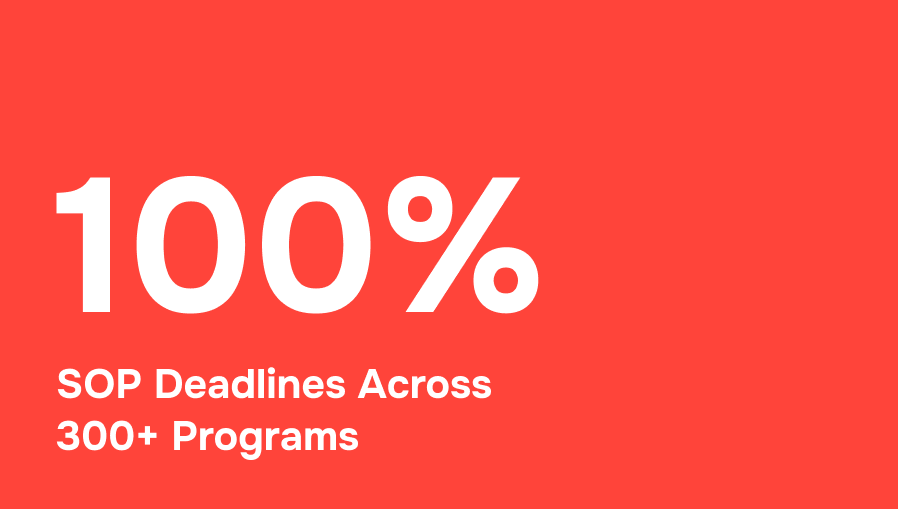
Build Responsive and Safe Robots
Maximize the full potential of your robotic systems with QNX® software that is trusted by manufacturers to support the expanding needs of the industry. Our foundational software is time-tested, performant, and safety-certified for embedded systems. We certified our QNX® OS for Safety and QNX® Hypervisor for Safety products to IEC 61508 SIL 3, and have launched both these products in the cloud to help optimize your development lifecycle.
Download our Robotic Solutions Guide to learn how QNX can help you realize the possibilities of your robotic applications.
Enabling Industrial Automation with QNX
Delivers foundational software that
- Optimizes overall performance of robotic systems.
- Increases system throughput, decreases processor utilization, minimizes jitter and latency, enables fault tolerant and fail-safe processes, adopts power-safe recovery, and reduce start-up time and energy consumption.
- Provides developer-friendly solutions for reducing development time and integration efforts.
- Is safety-certified to IEC 61508 SIL 3.
- Relieves end system certification burden.
Build Responsive and Safe Robotic Systems
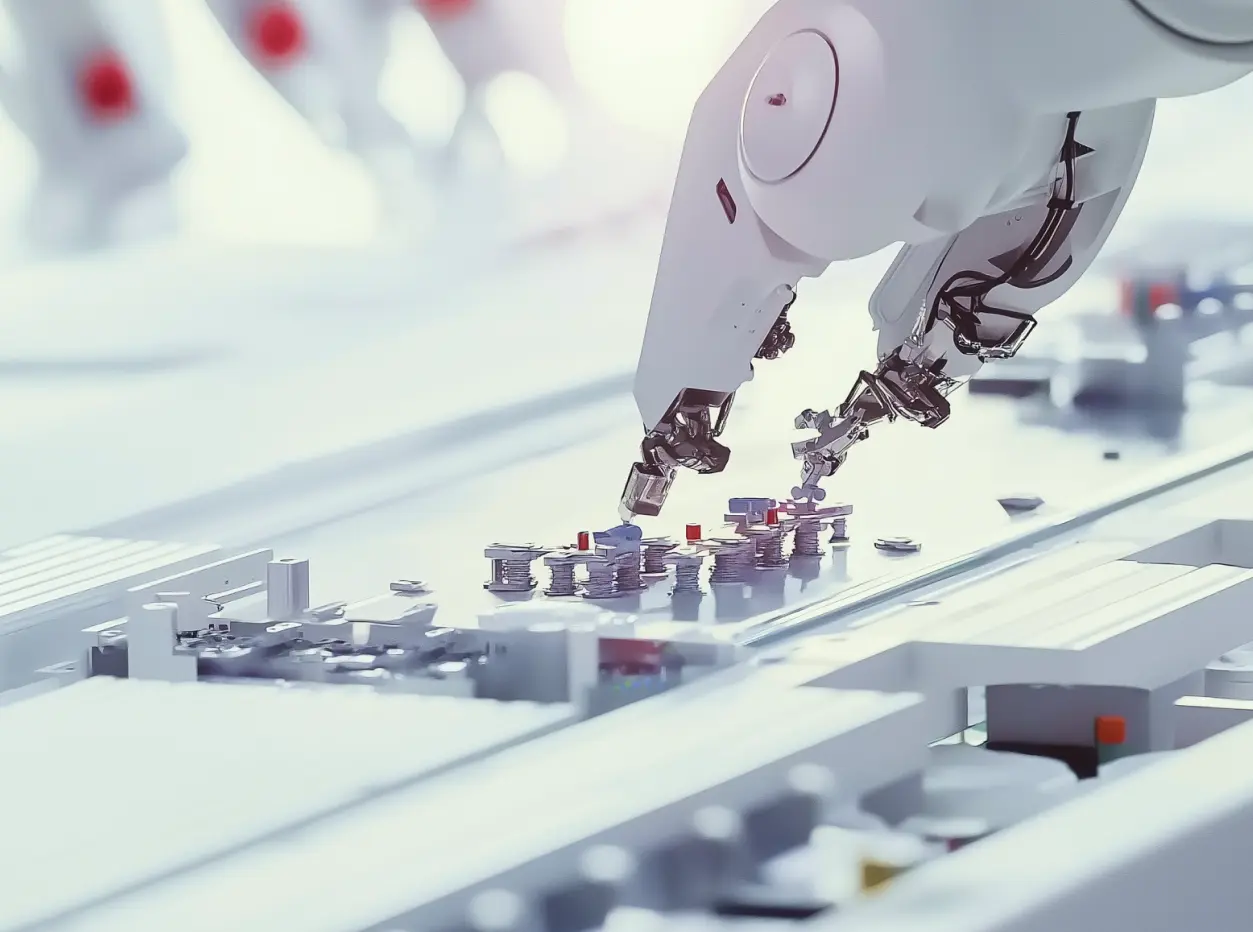
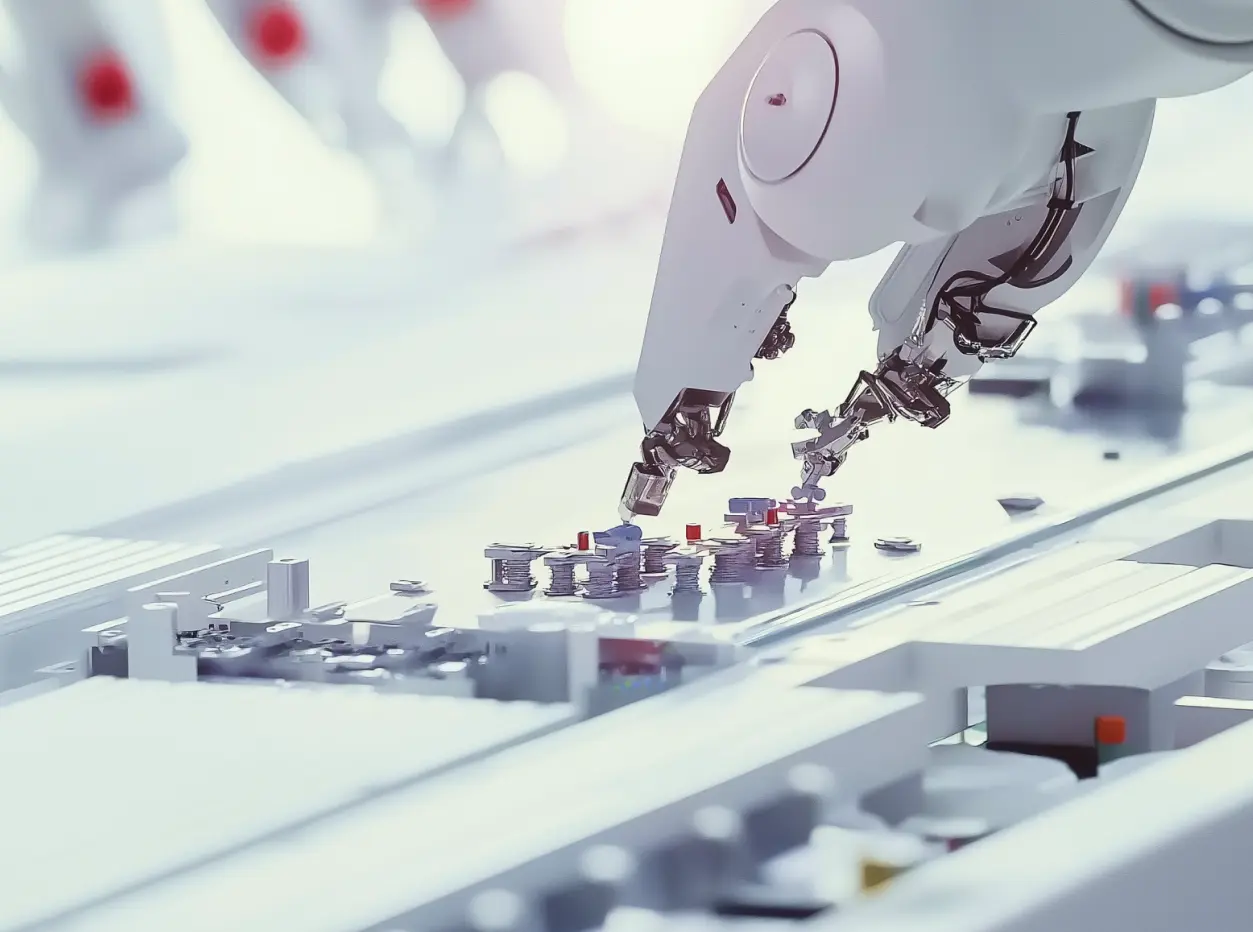
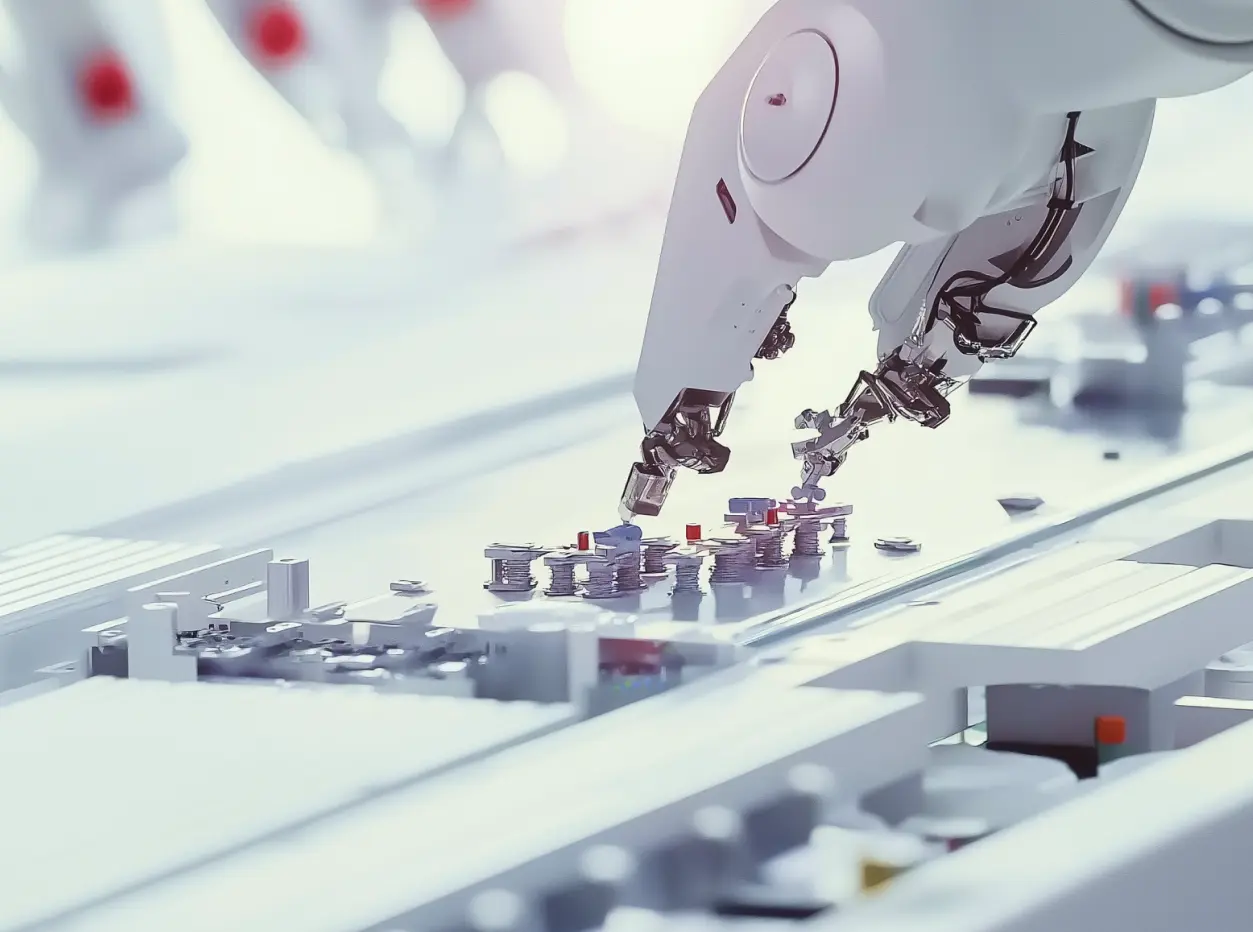
Optimize Performance
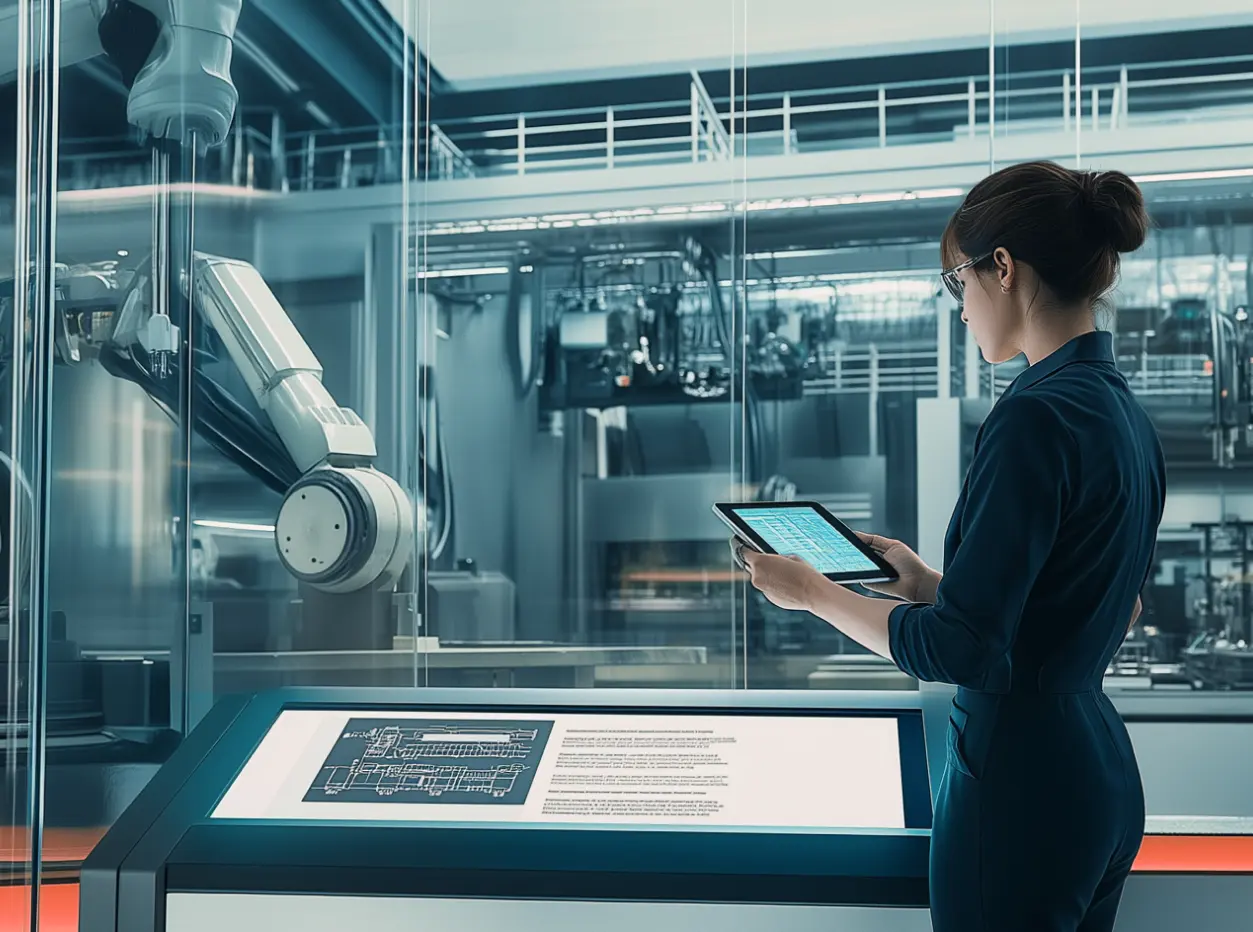
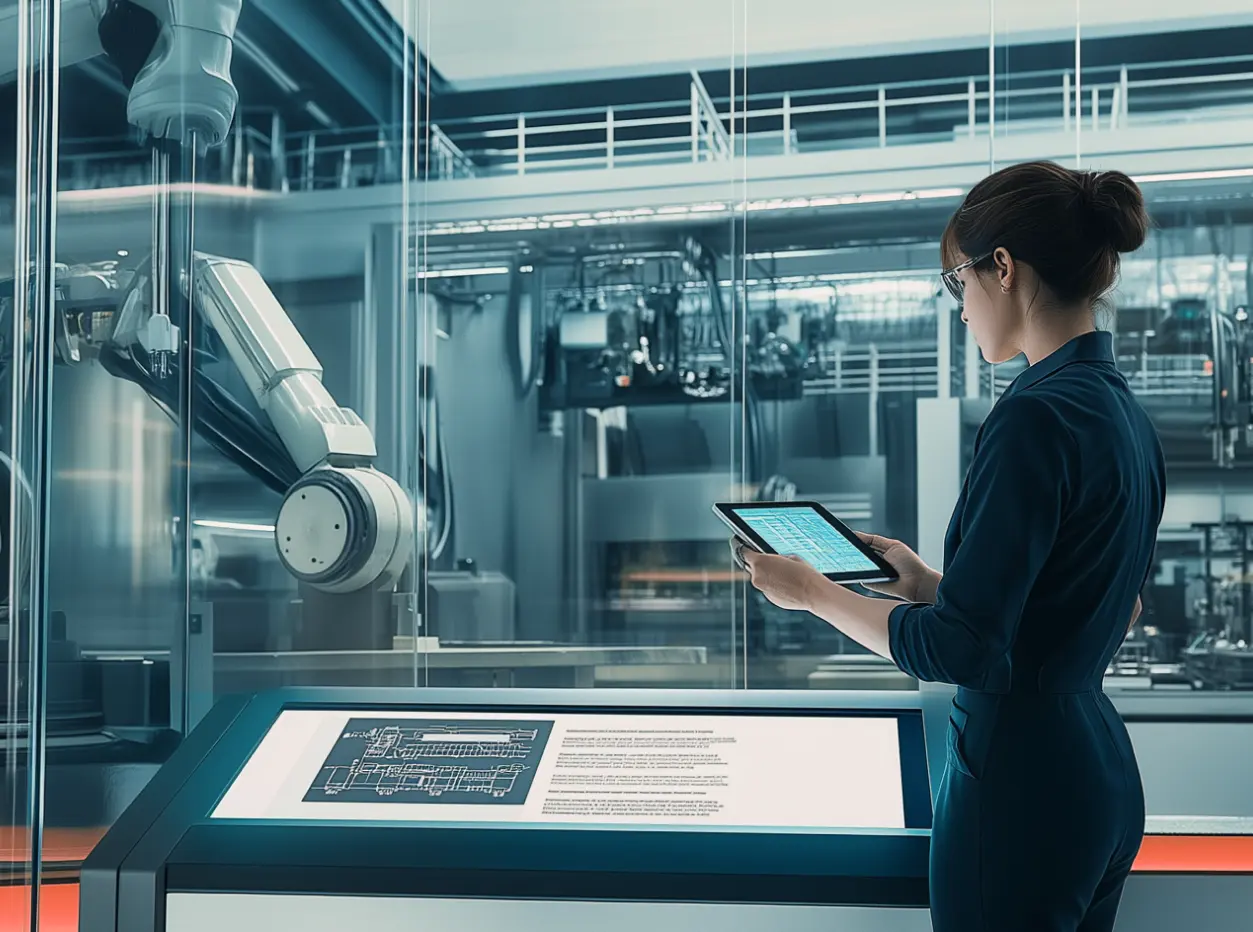
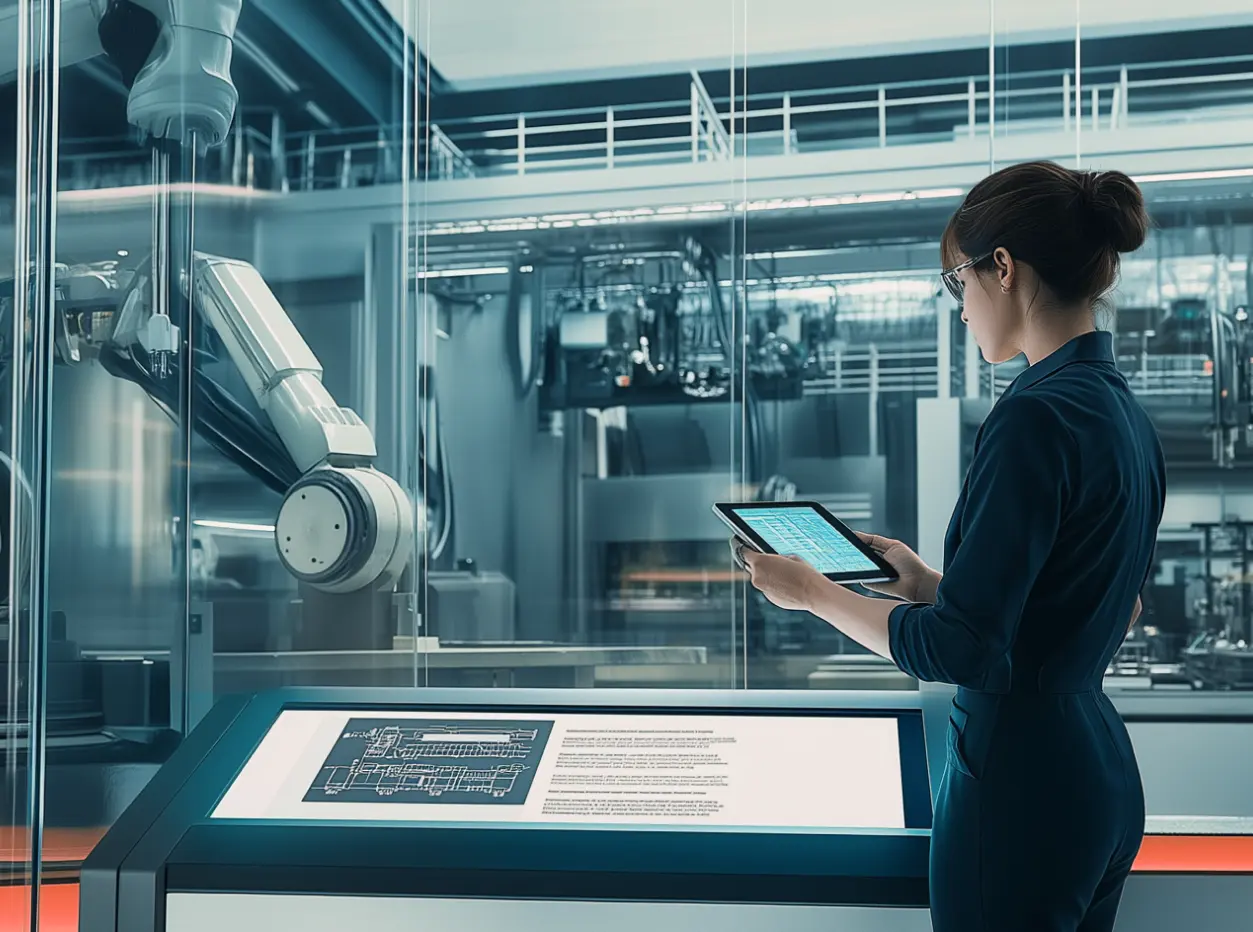
Functional Safety
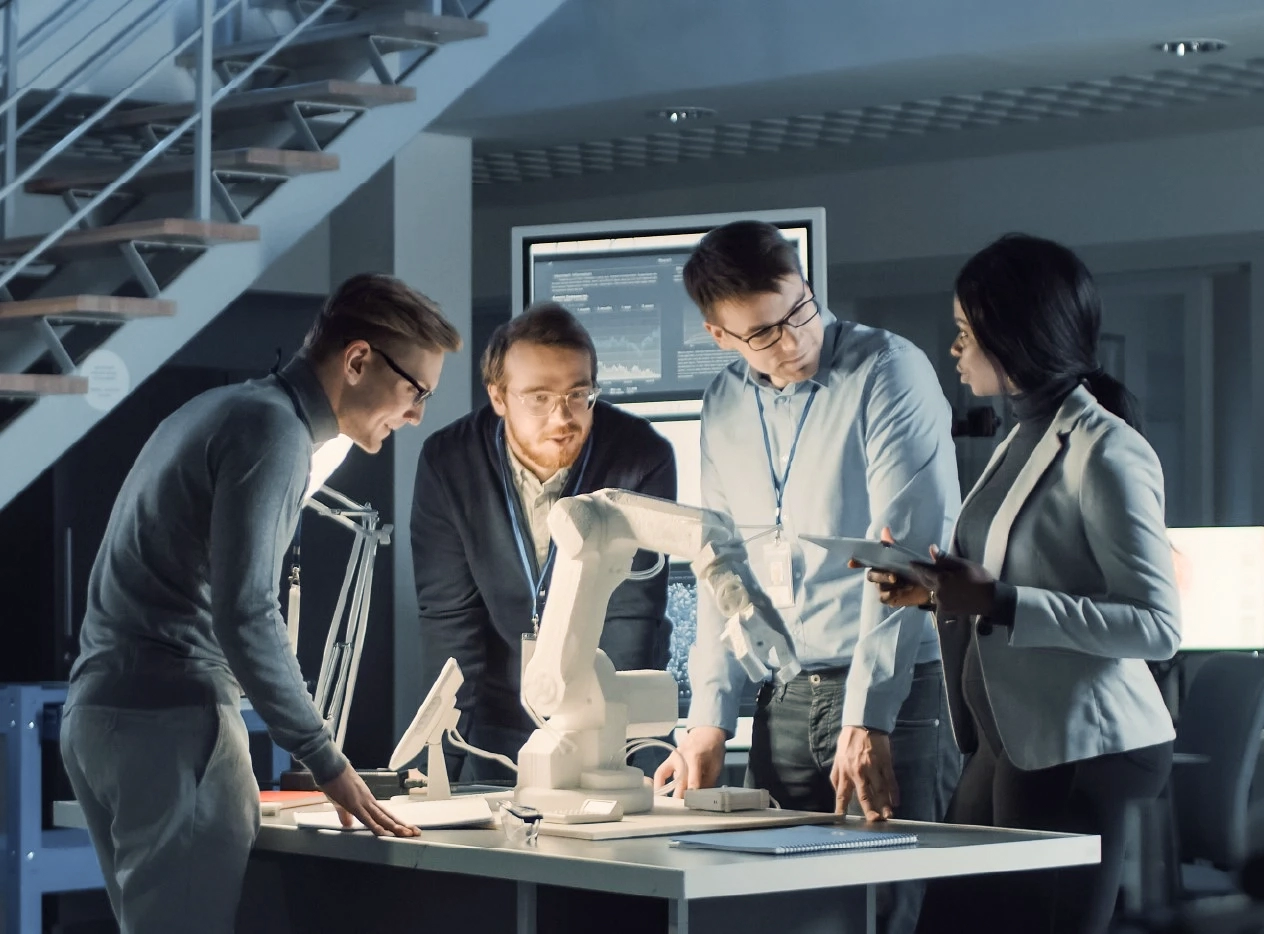
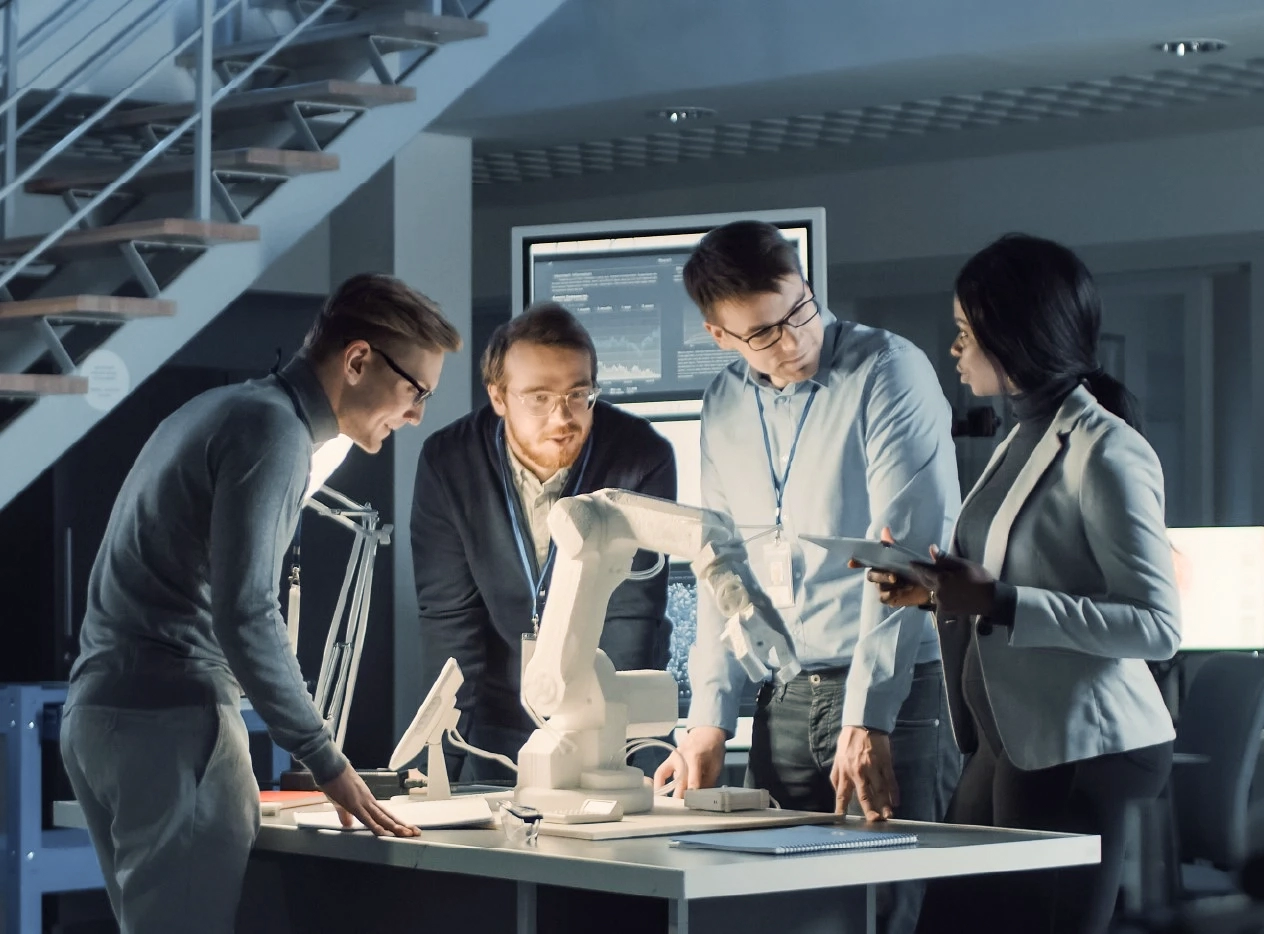
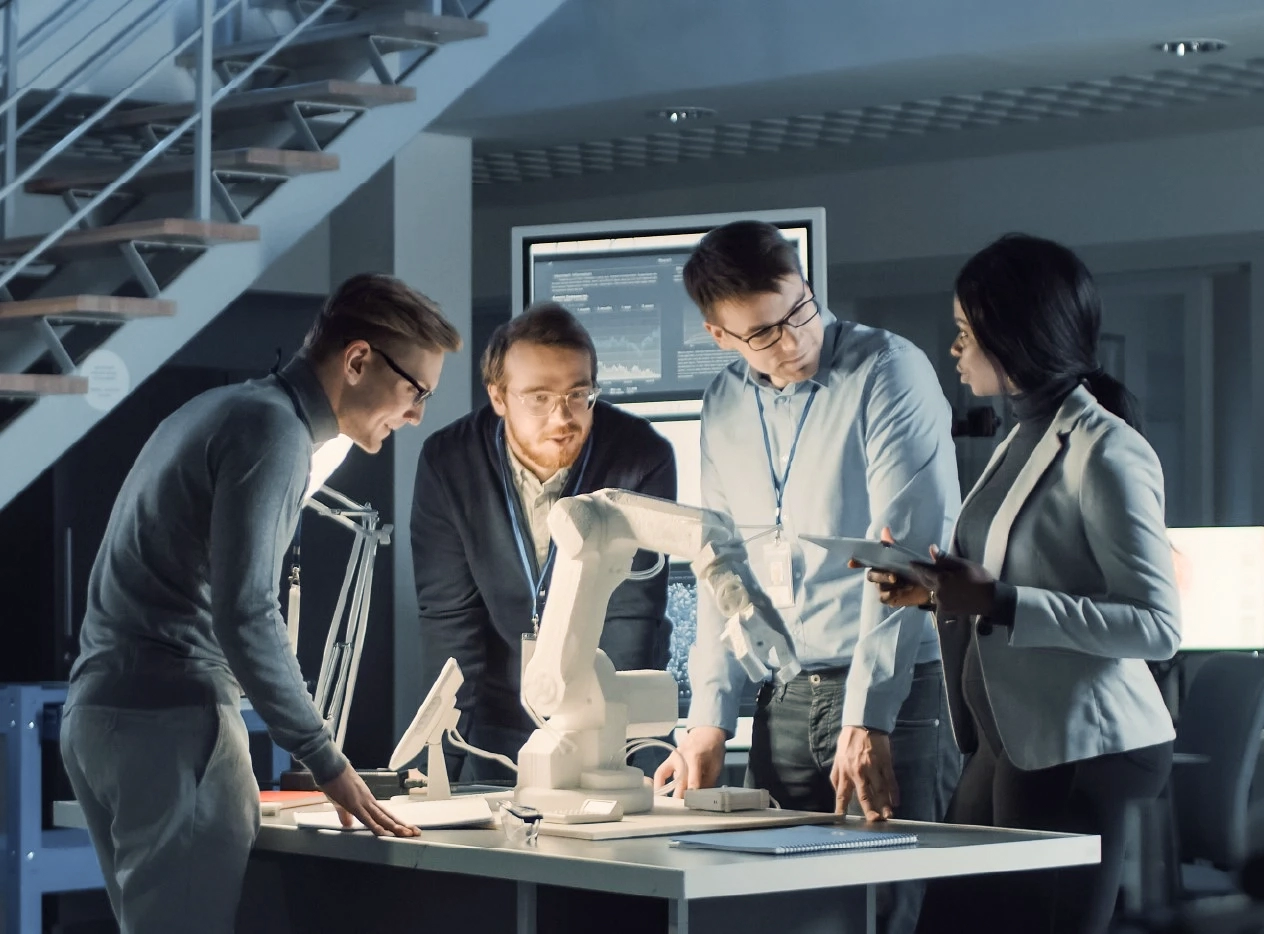
Simple to Build
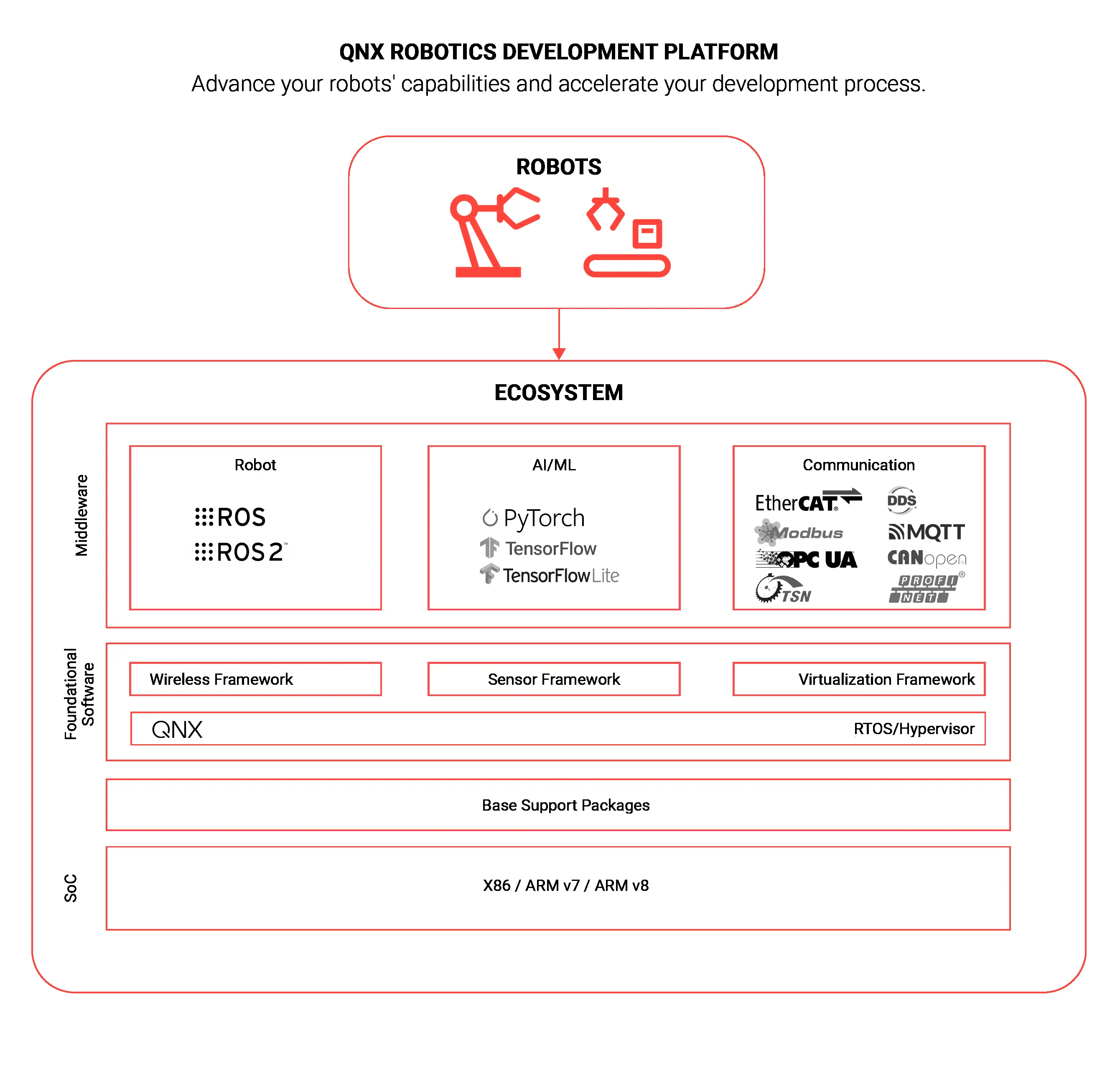
Advancing Robotics – Software Solutions for Building and Deploying High-Performance Systems
Hard Real-Time Performance for Robotic Systems
QNX® OS 8.0 is the next-generation hard real-time operating system that enhances overall robotic systems performance. It provides the unique characteristics of predictability and determinism to minimize latency and jitter needed to reliably enable robots across various industries and applications.
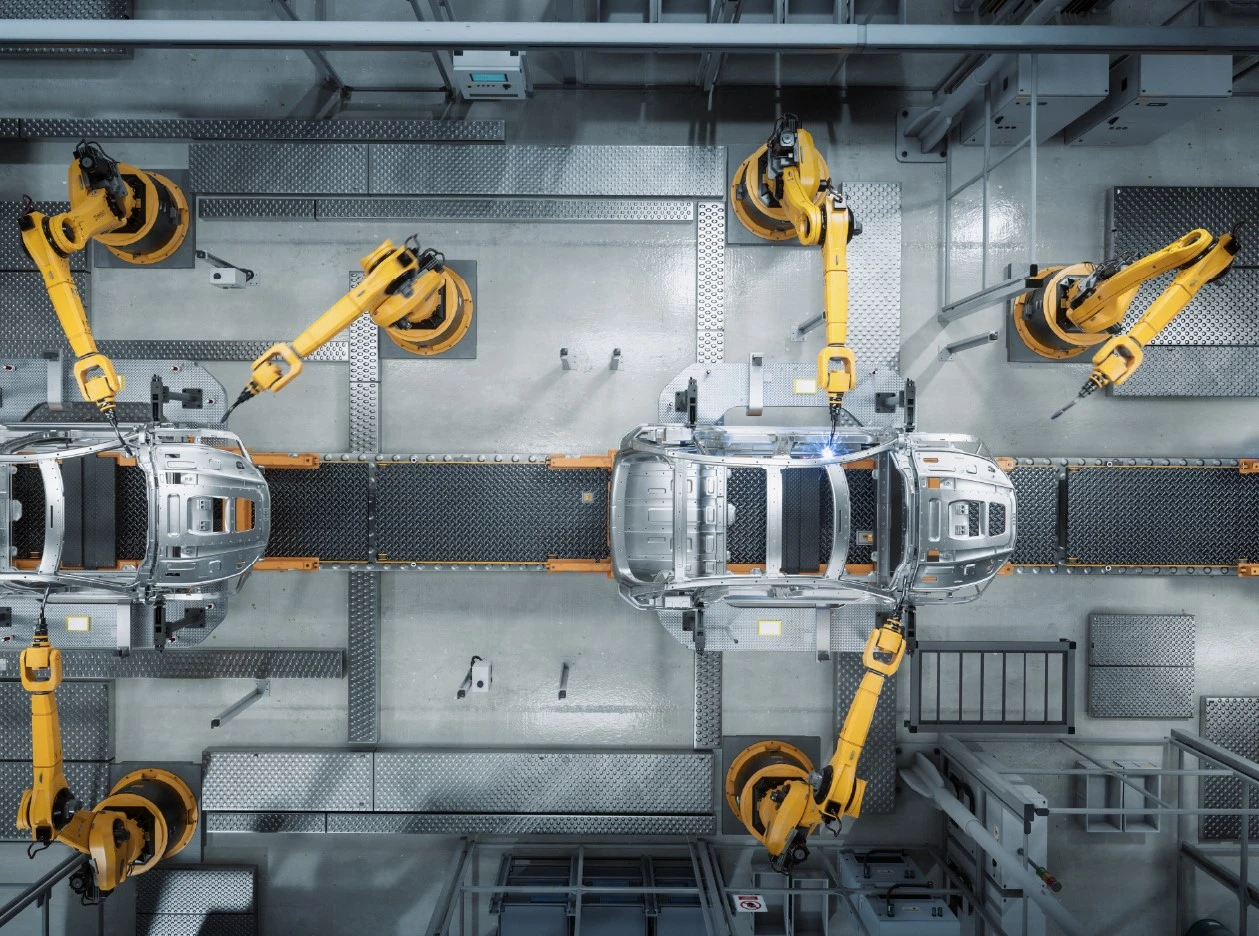
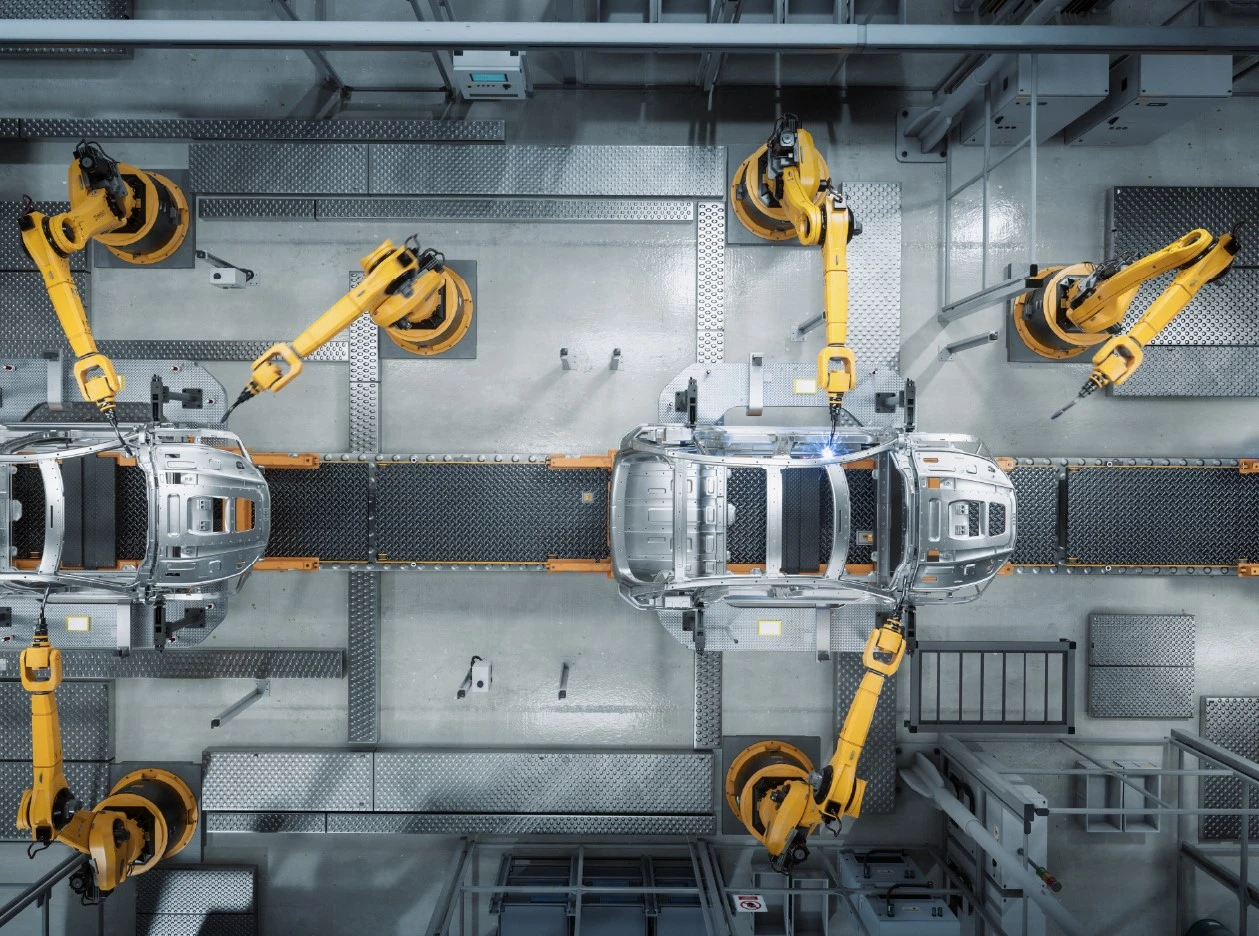
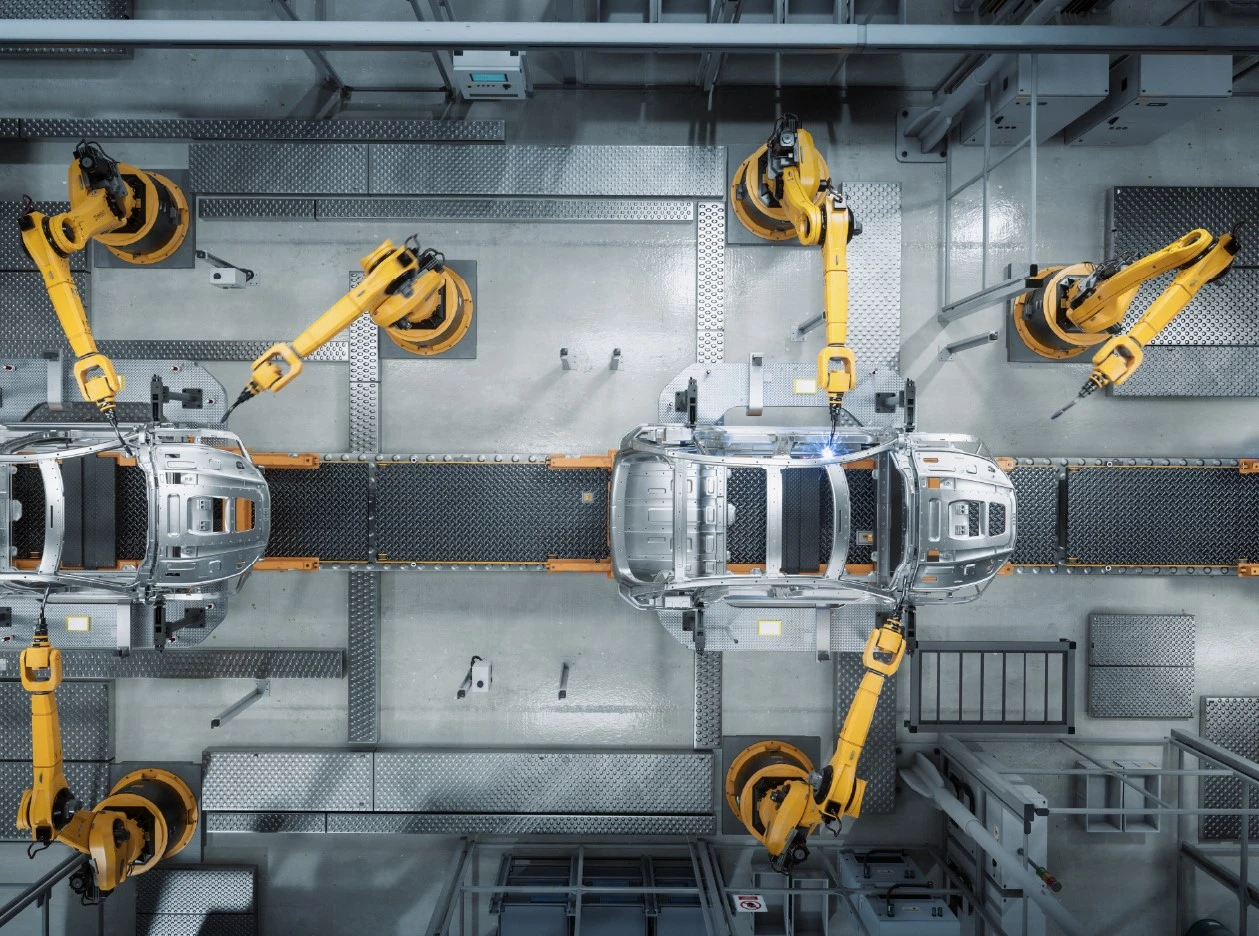
Manufacturing
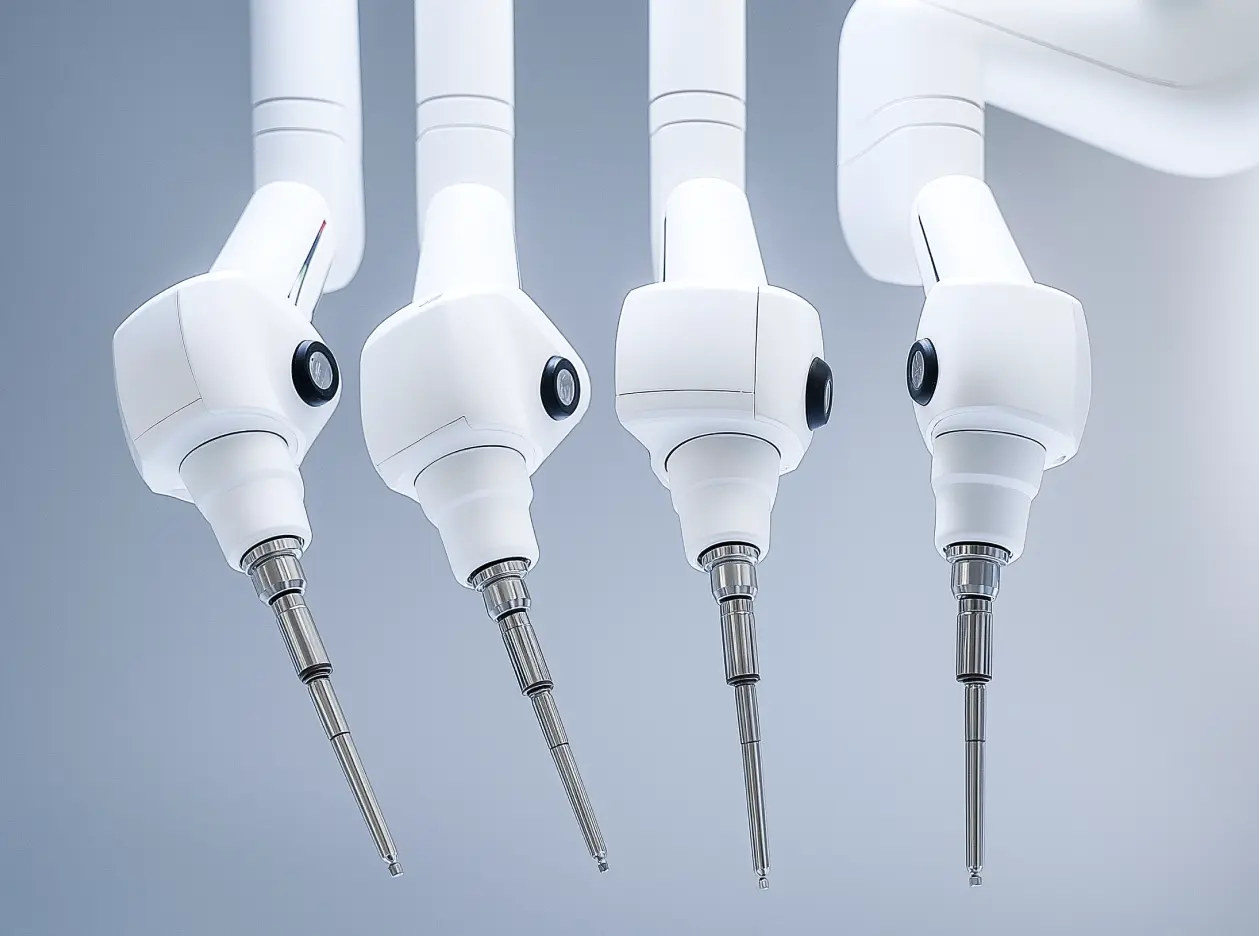
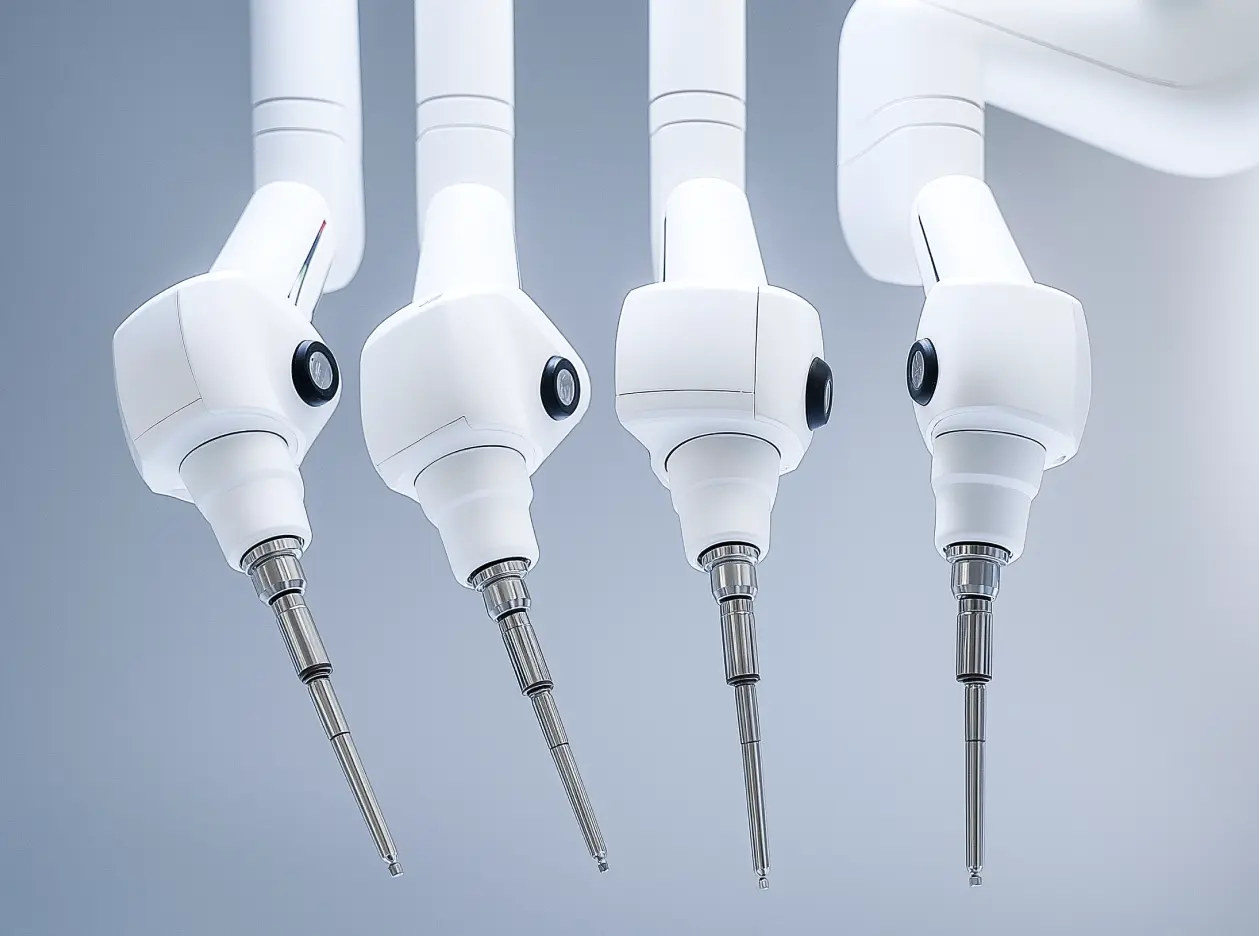
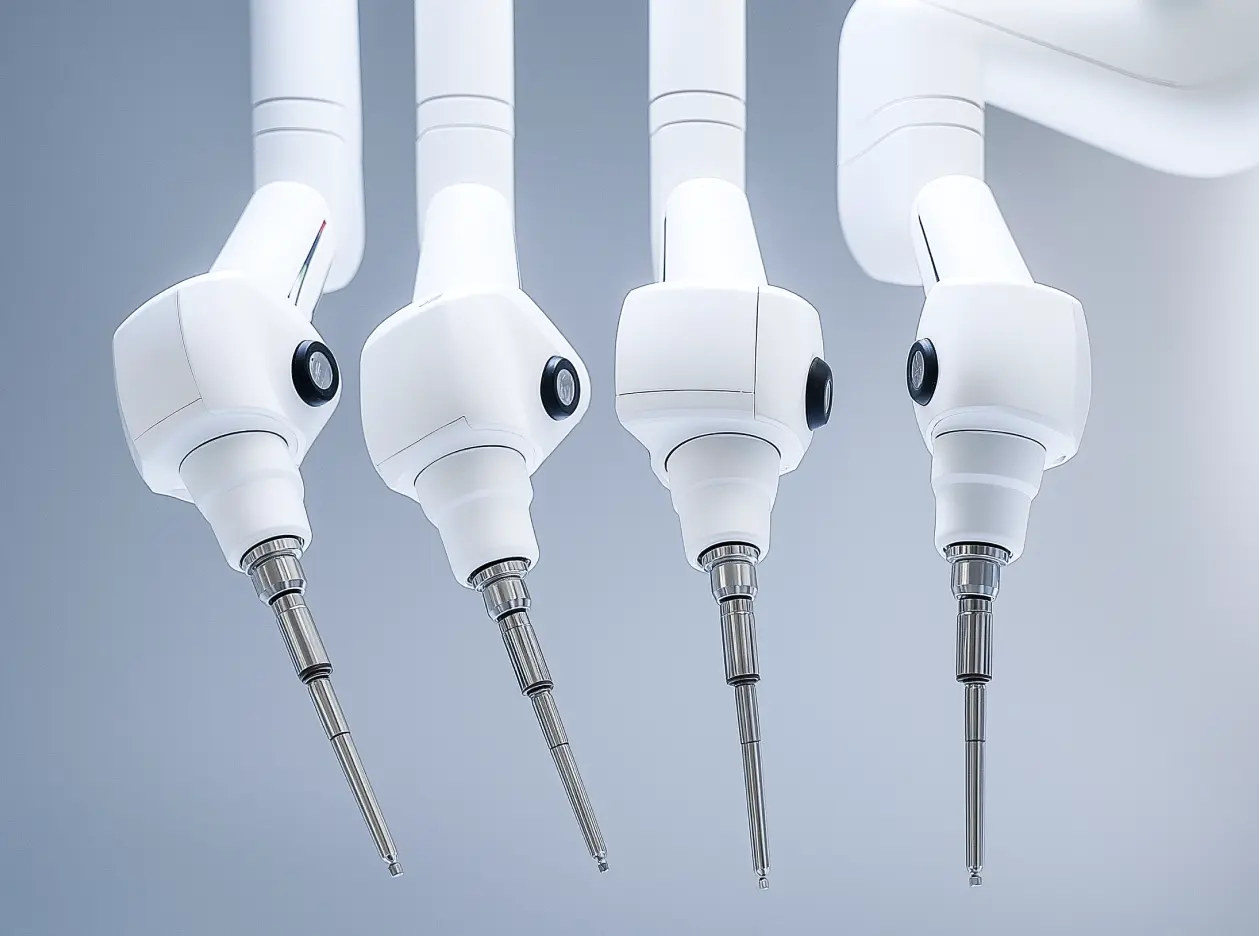
Surgical
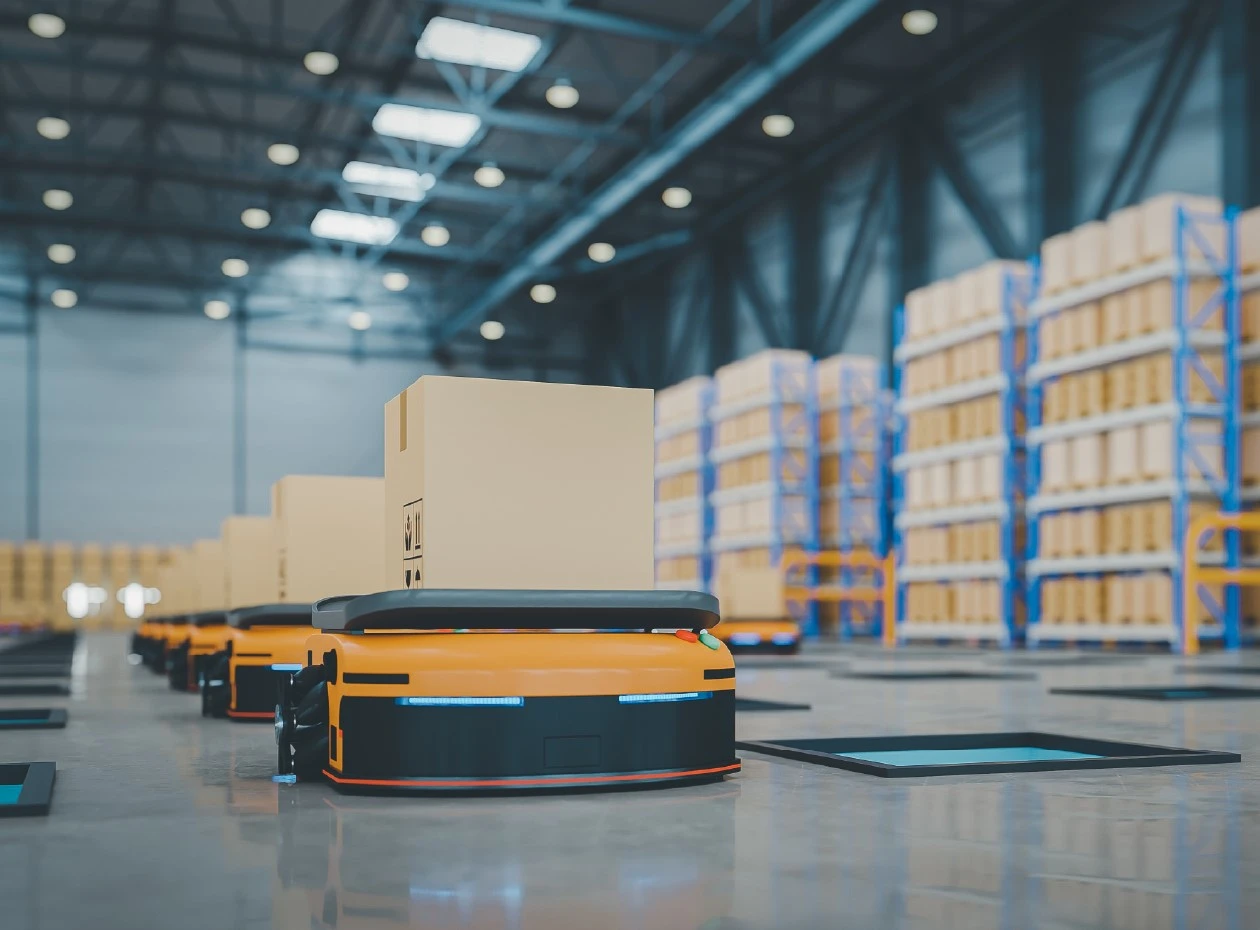
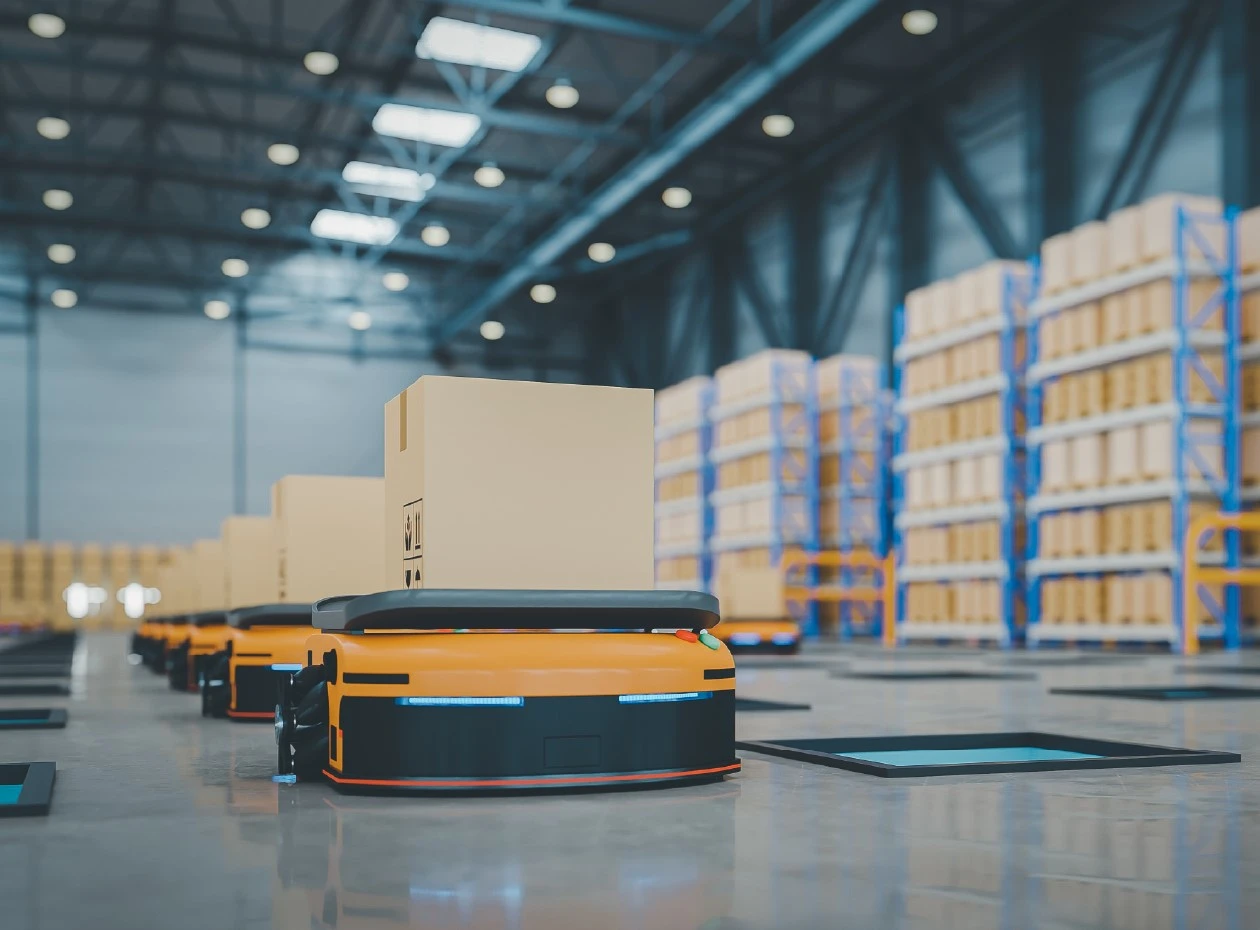
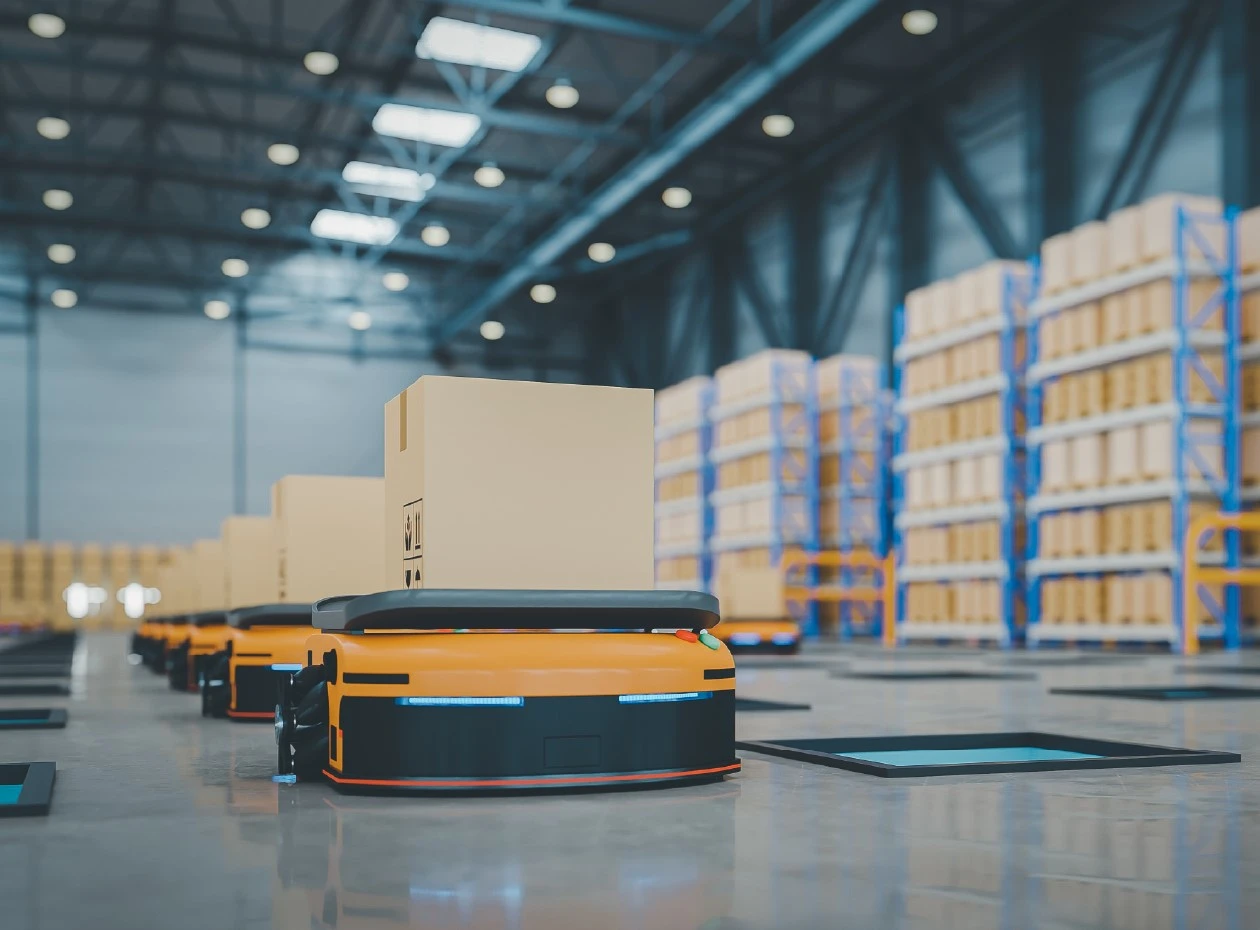
Logistics and Warehouse
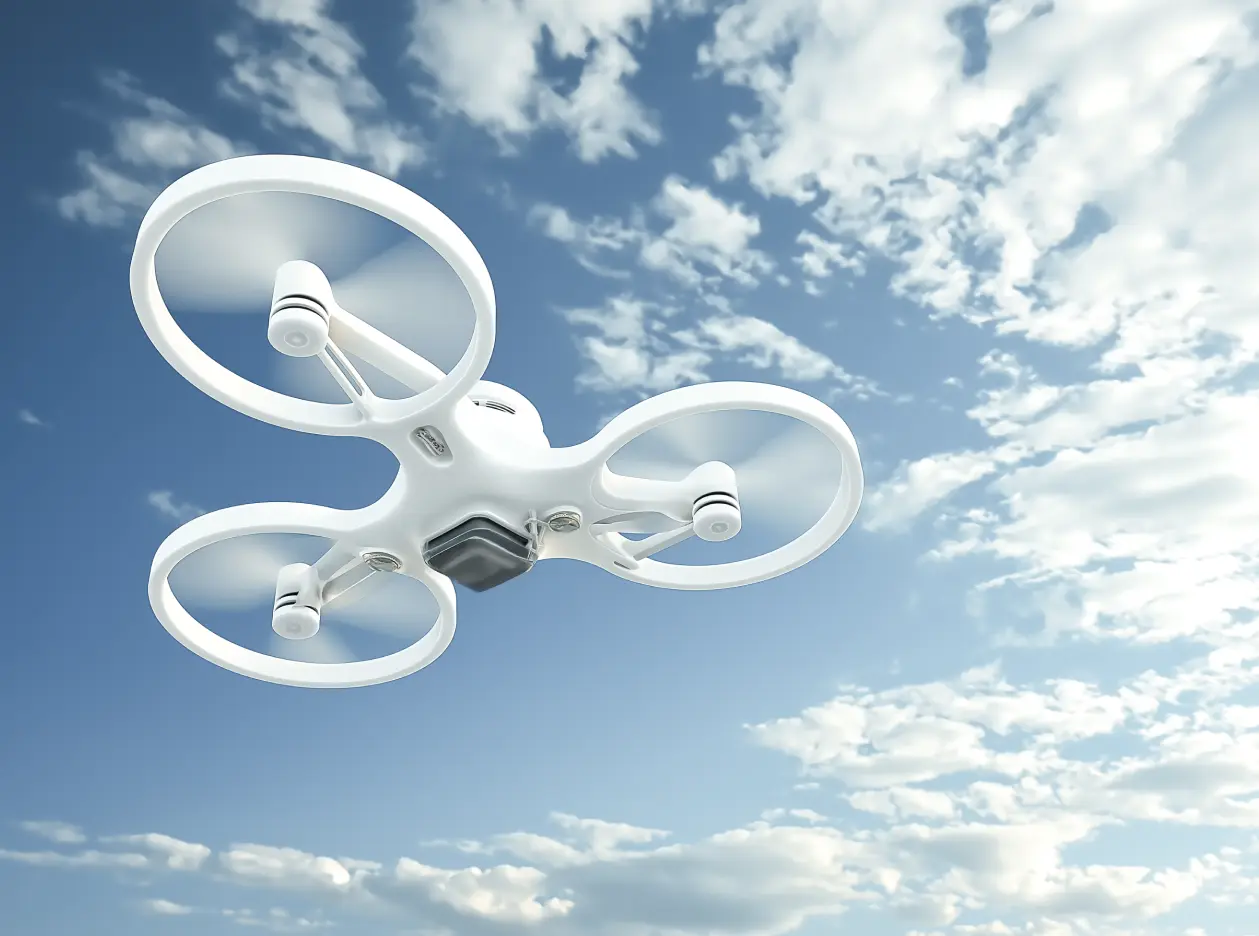
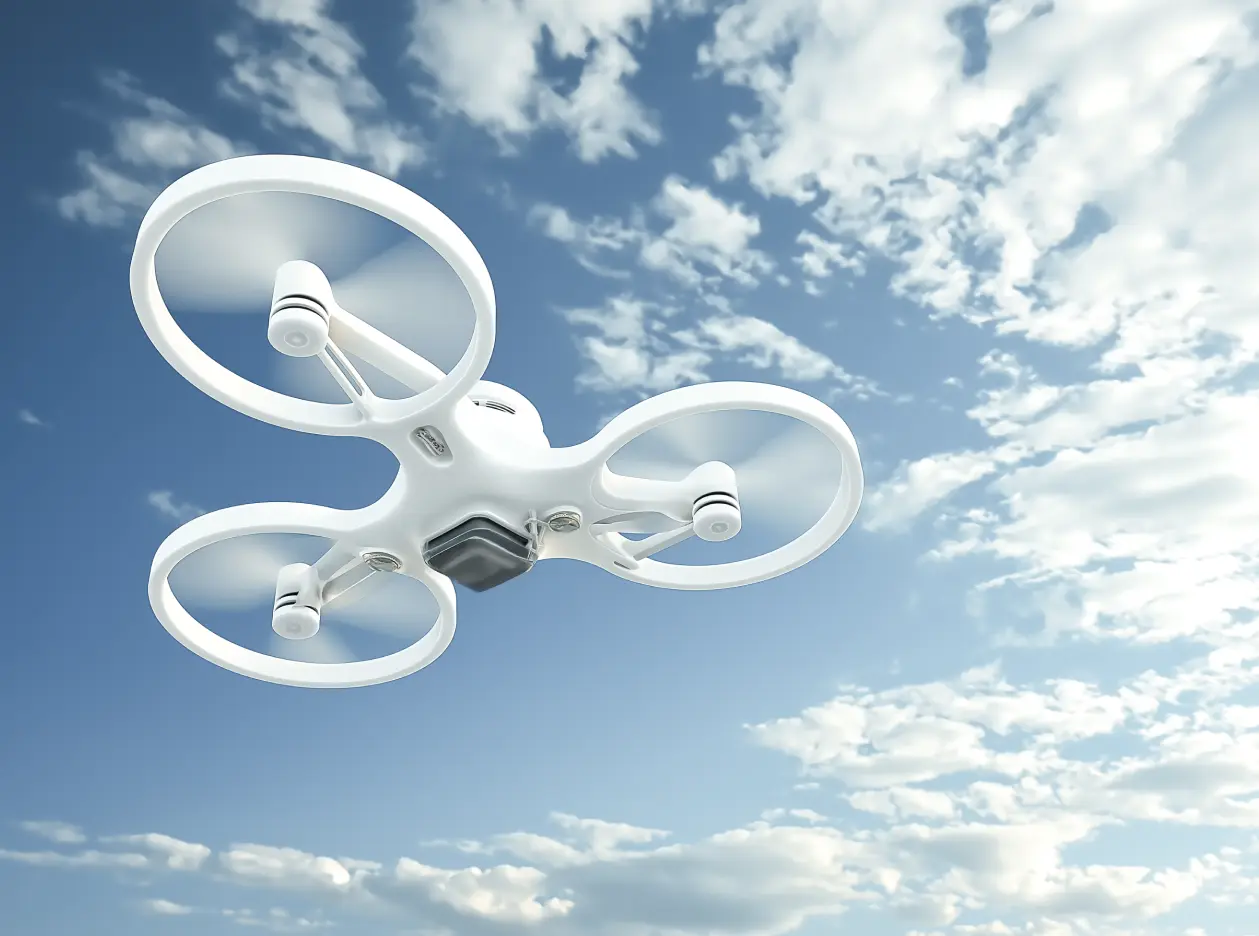
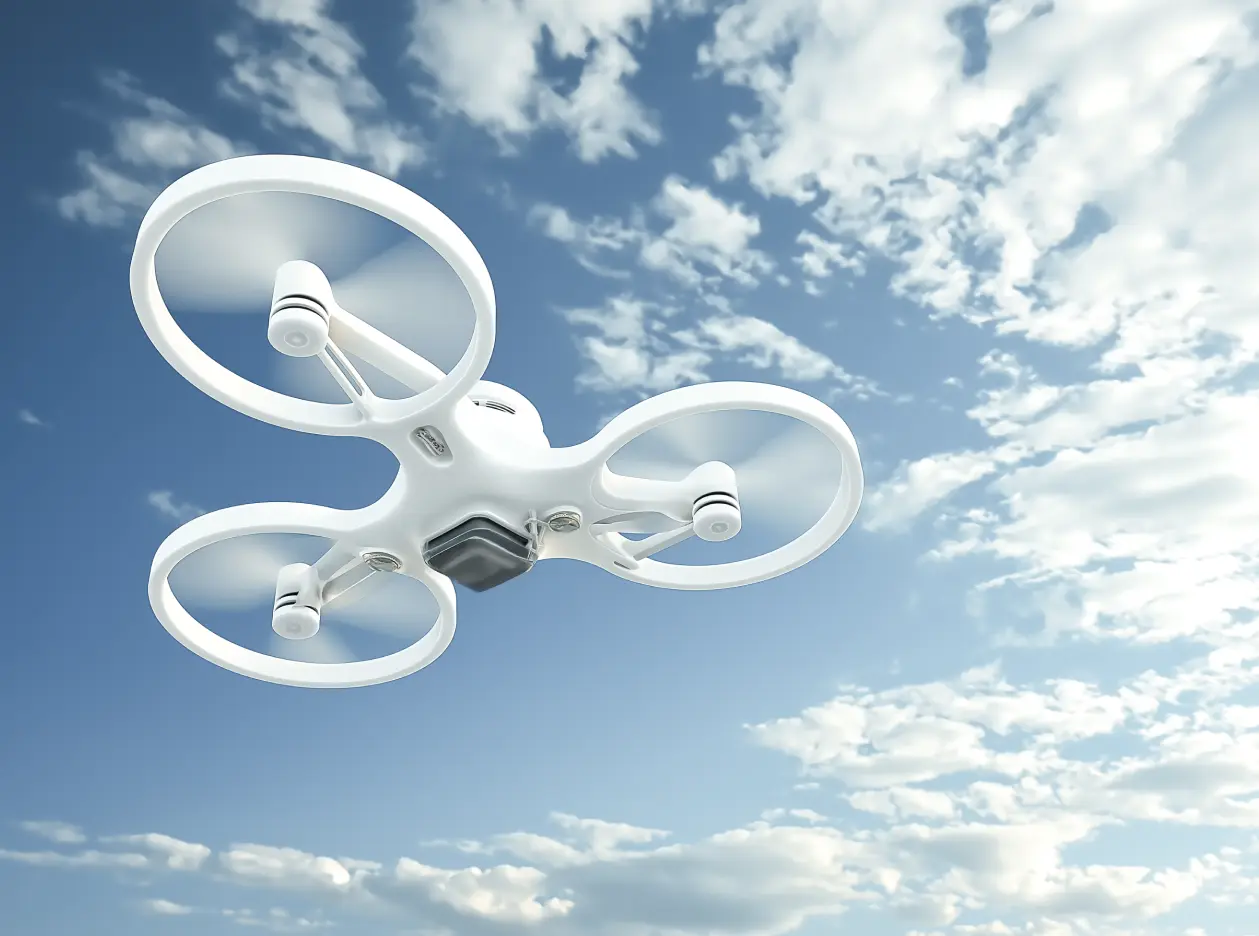
Defense

Precision in Robotics
Related Solutions
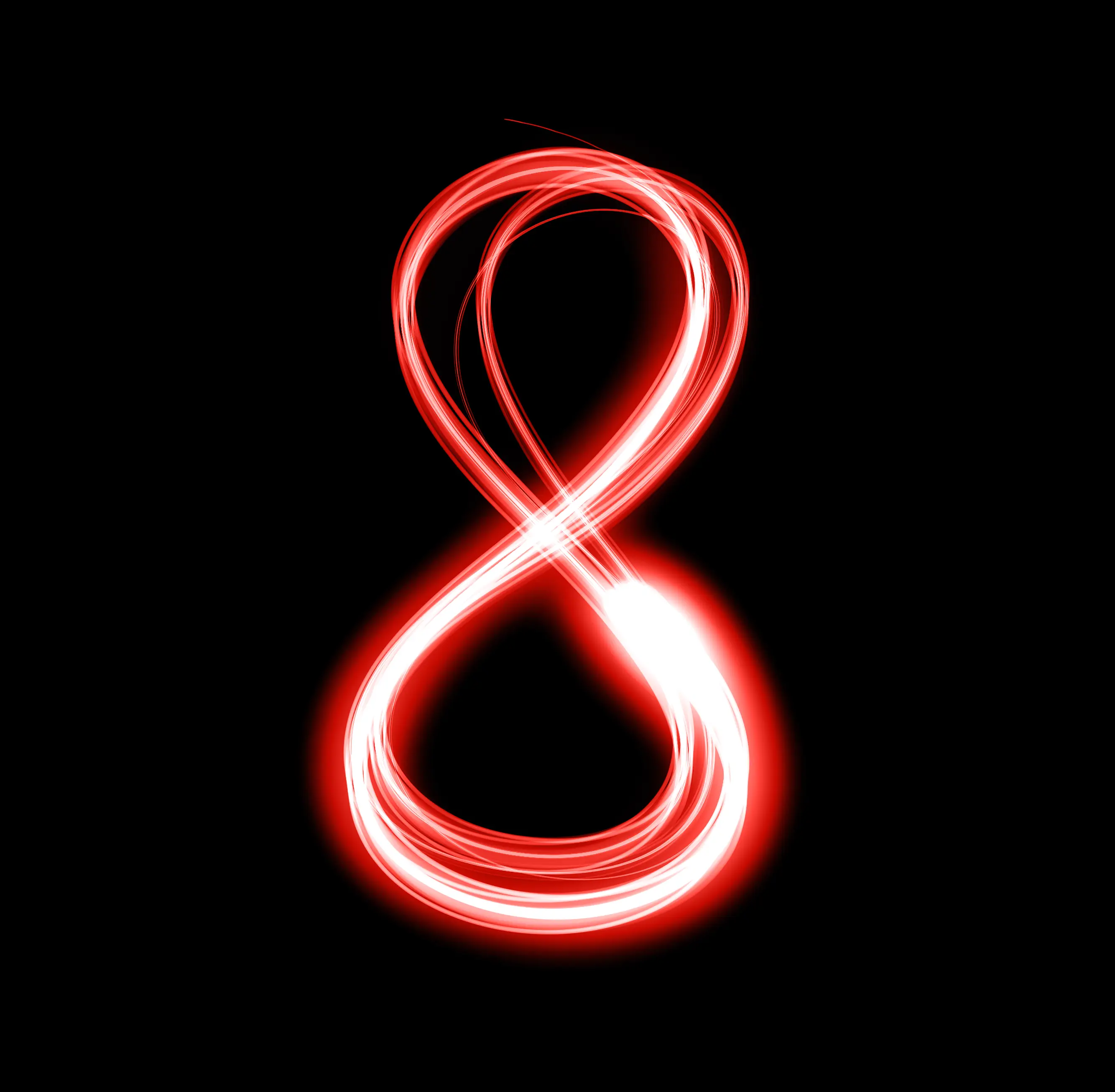
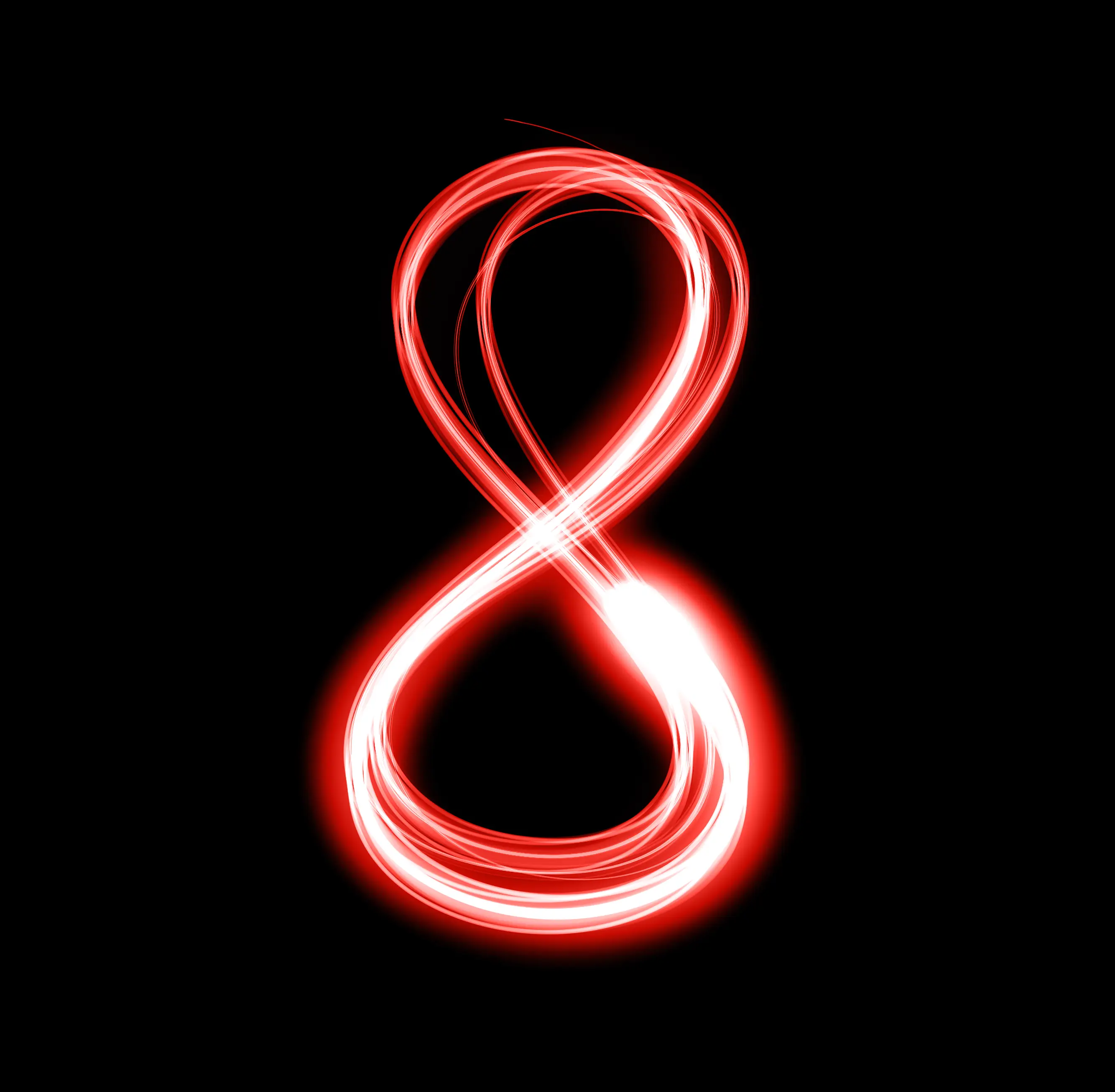
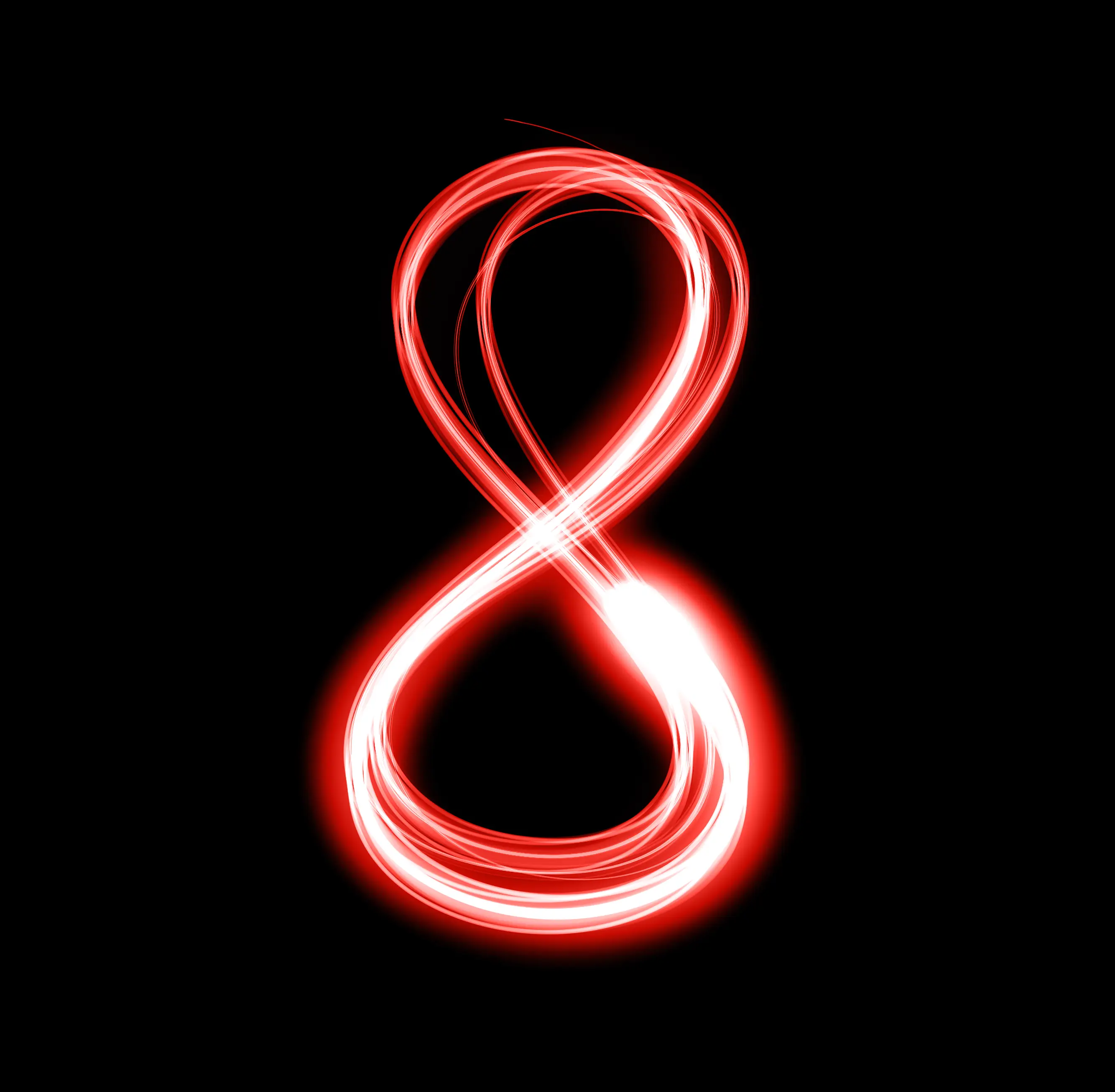
QNX SDP 8.0
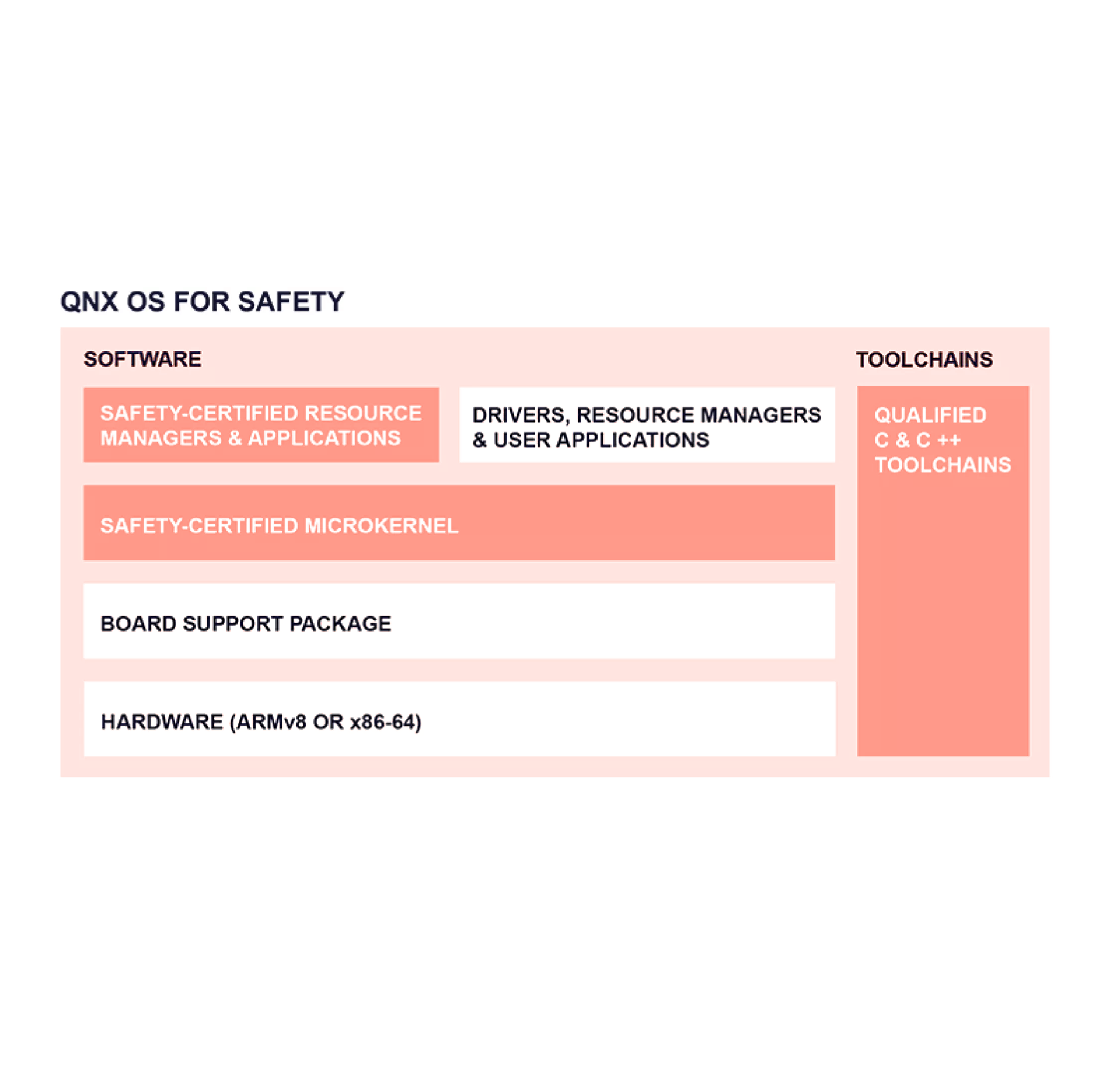
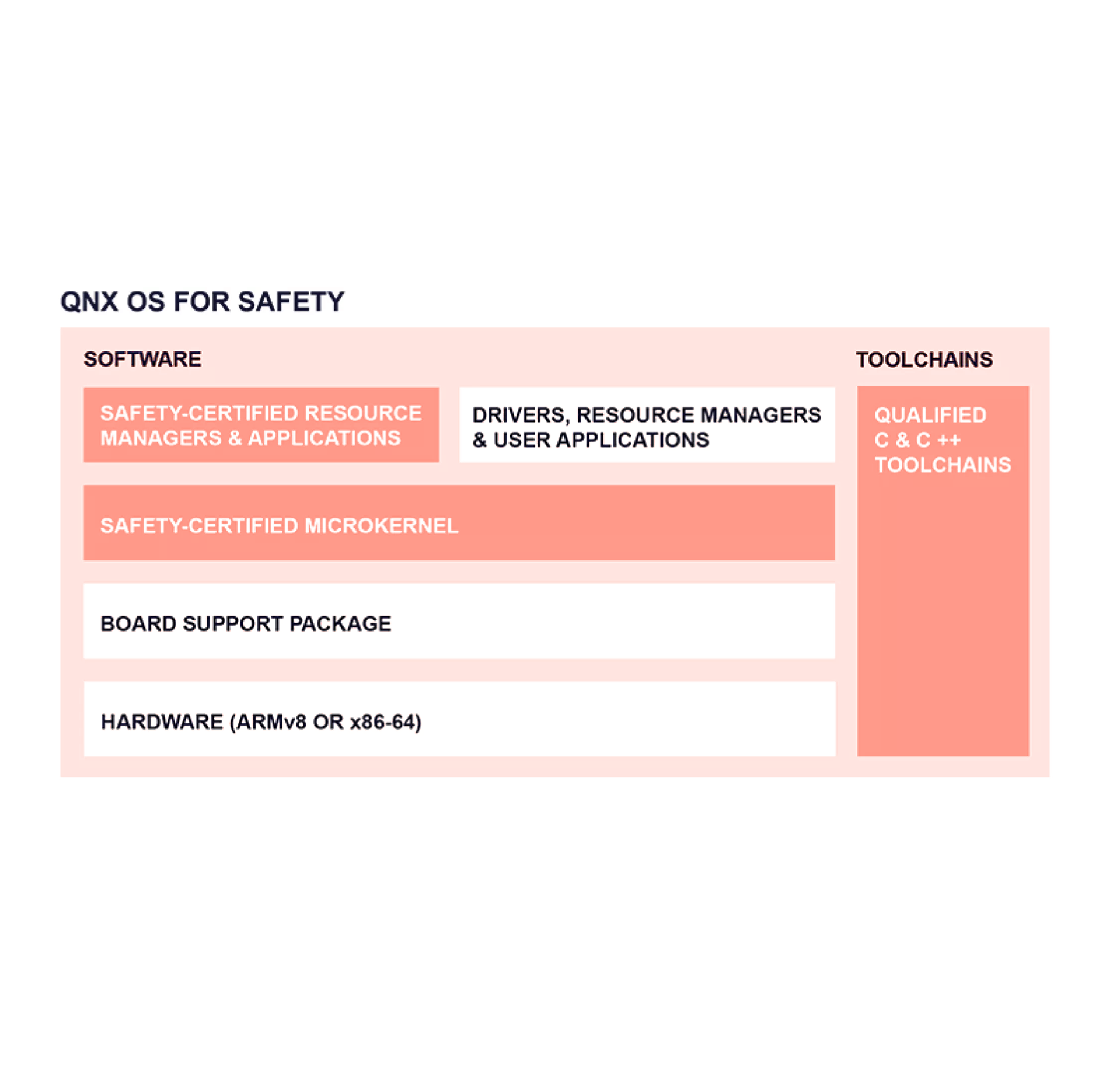
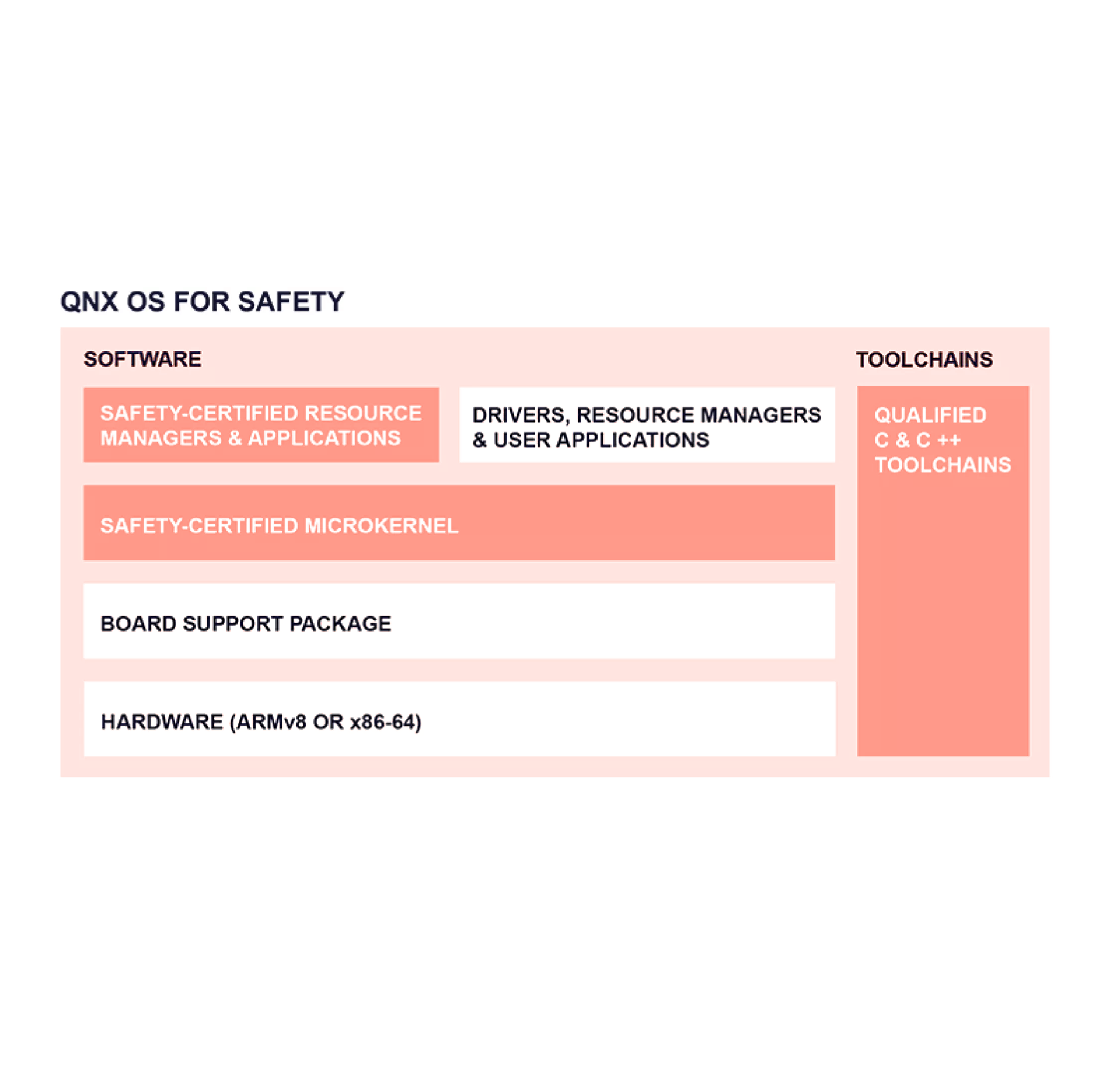
QNX OS for Safety
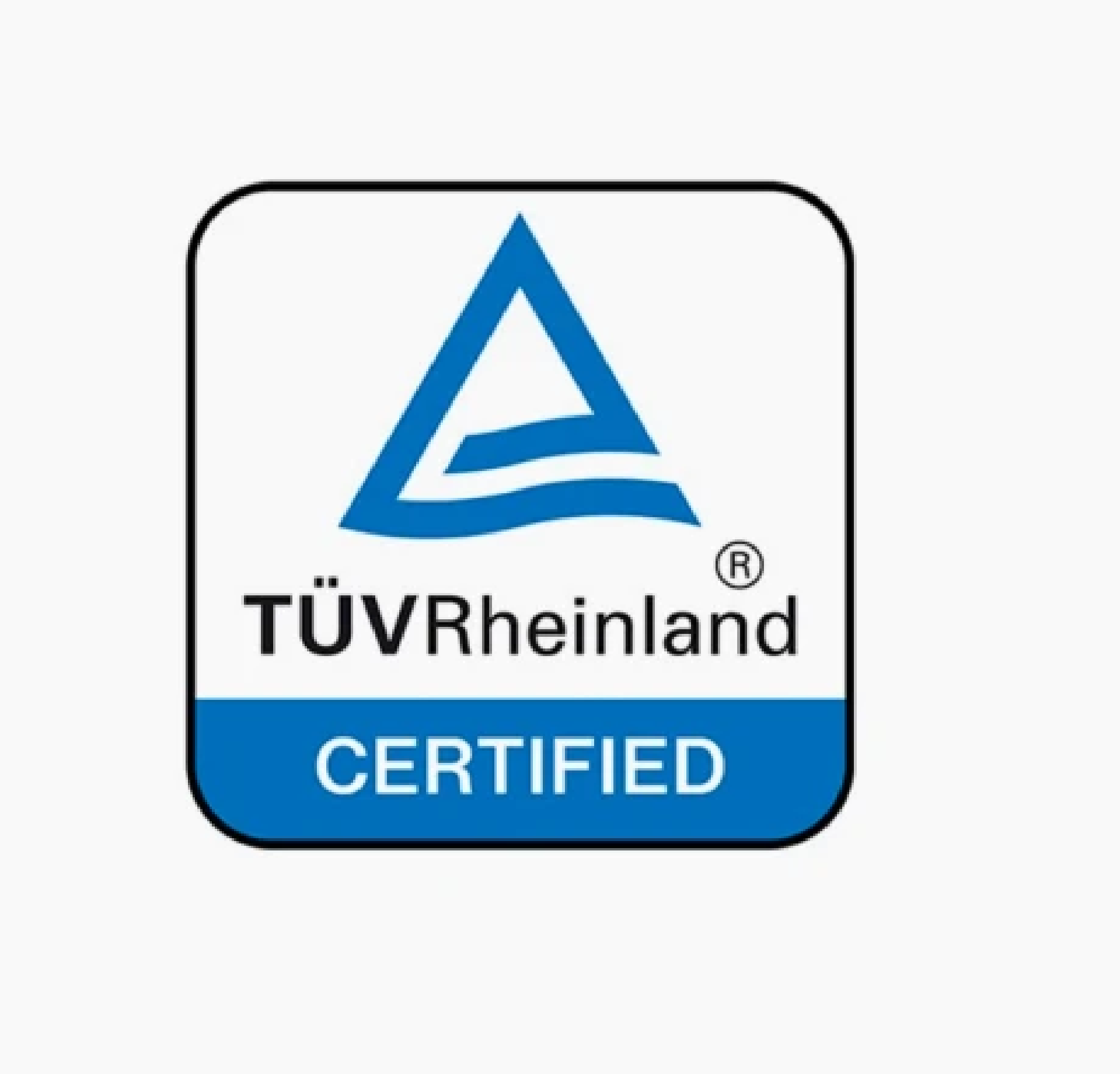
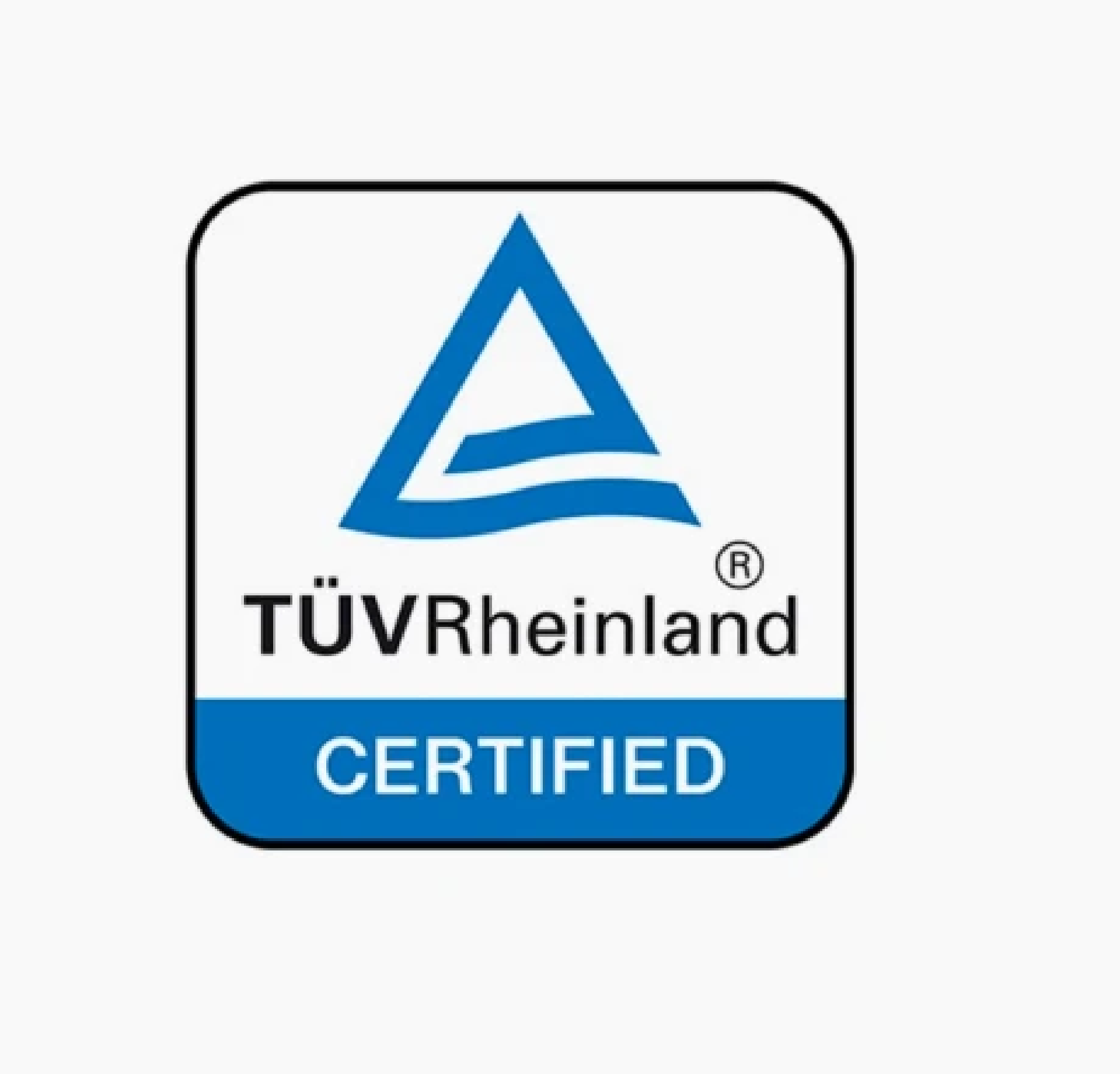
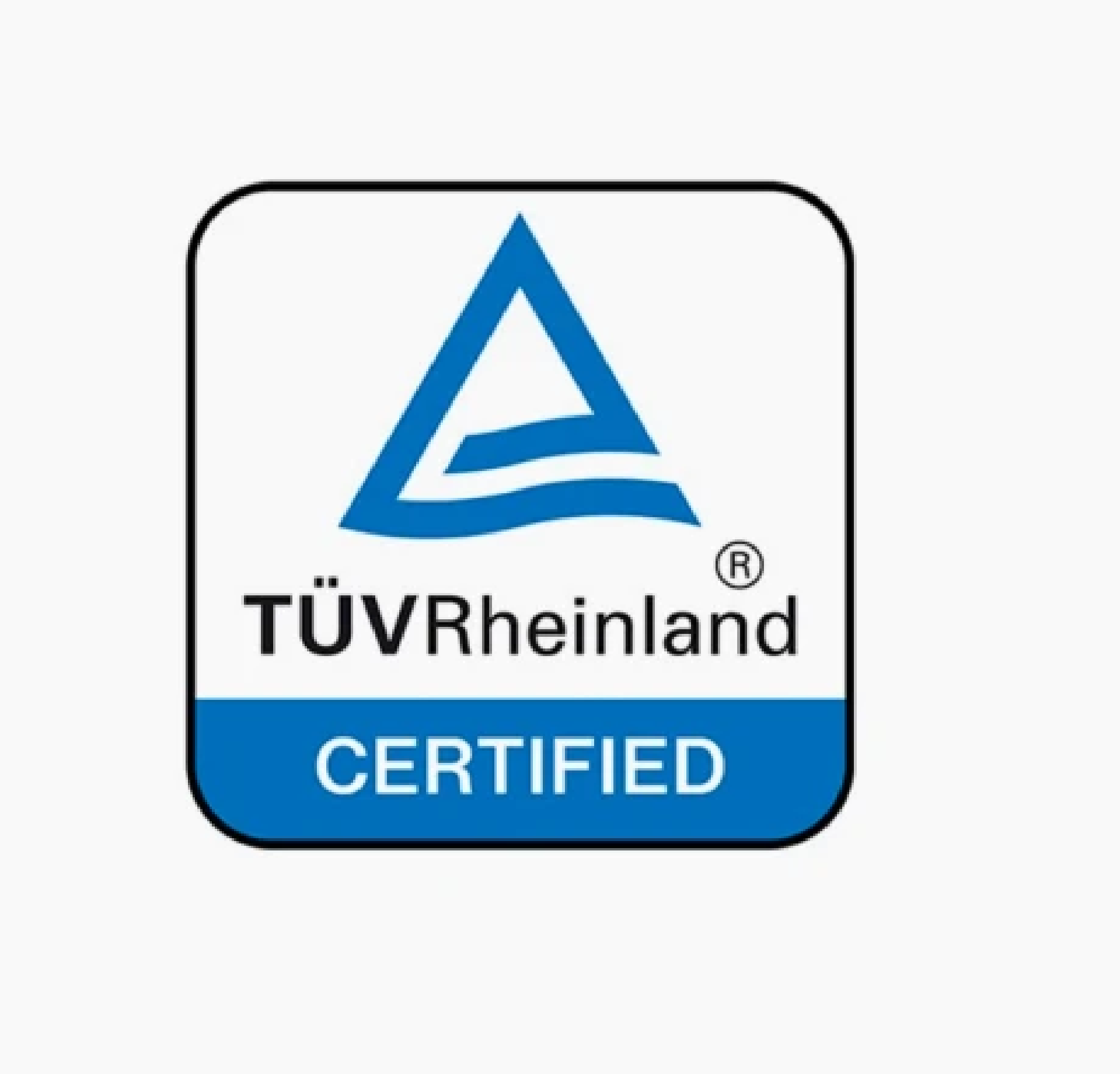
QNX Hypervisor for Safety
FAQs about QNX for Robotic Software
Which products are currently safety-certified to IEC 61508 standard?
The QNX OS for Safety and QNX Hypervisor for Safety are certified to IEC 61508 SIL 3. QNX® Hypervisor for Safety offers the same trusted functionality and performance as QNX® Neutrino® real-time operating system (RTOS) plus virtualization support. These products are safety-certified variants of the QNX Neutrino RTOS and the QNX Hypervisor, respectively.
What are the benefits of a safety-certified RTOS?
Building a safety-certified robotic system with a pre-certified RTOS allows you to focus on the higher-level components of the system, greatly reducing the certification process of the end-system. More benefits of a safety-certified RTOS such as the QNX OS for Safety include:
- Reduced development effort. QNX documents safety recommendations and restrictions to reduce the time and effort (e.g., testing, analysis, documentation) needed for you to develop these materials from scratch—not to mention enables you to design a safe system using these guidelines.
- Reusable code. Build a platform and reuse it across your entire product line with little integration effort.
- Accelerated time-to-market. The development process can be streamlined to leverage QNX safety artifacts for quicker approvals from regulatory bodies.
- Maintenance and support. QNX products are maintained and supported throughout the product lifecycle with the utmost rigger, allowing you to focus your efforts on your applications and not the software it’s built on top.
- Cost savings. The cost of purchasing safety certification documents can be reduced as it relates to documentation development time and testing efforts. This cost is amplified if there are product updates that require resubmission of documentation.
How does QNX support the pending changes to ISO 10218-1 and ISO 10218-2 standards?
Updates to ISO 10218 part 1 and part 2 standards for industrial robots are anticipated to be released with new functional safety requirements. These changes could standardize the industry’s safe integration for collaborative applications between robots and human workers. Added safety features are anticipated to be more software-defined and could require conformance up to IEC 61508 SIL 3.
How easy is it to develop with QNX?
QNX foundation software solutions are POSIX-compliant and will be familiar to anyone who’s worked with the Linux® operating system. Purpose built for sophisticated embedded devices like robotic systems, the QNX® Software Development Platform (SDP) 8.0 includes the latest QNX OS 8.0, QNX® Tool Suite (including QNX® Momentics® IDE our Eclipse-based integrated development environment, QNX® Toolkit for Visual Studio Code, and command line tools) and the QNX Software Center to provide a full-featured, microkernel RTOS for ARM and x86 platforms with 64-bit support. It also includes a High-Performance Networking stack to support basic-to-complex networking requirements.
Is ROS and ROS2 available on QNX?
Robot Operating System (ROS) and ROS 2 have been ported to and are available on QNX foundational software solutions. This allows you take full advantage of the benefits of our products while using ROS and ROS 2 to handle the communication between robotic components such as vision systems, speech recognition modules and actuator controls.
Can I build machine learning (ML) and artificial intelligence (AI) applications with QNX?
To accelerate the development of ML and AI applications for the intelligent edge, popular AI frameworks such as TensorFlow, TensorFlow Lite, and PyTorch are available with QNX products. The combination of these AI and ML frameworks on the QNX real-time operating systems enables you to build advanced features, such as digital twins for manufacturing sites that enable real-time processing on both the devices and in the cloud.
What communication standards and protocols are available with QNX?
Through our vast network of ecosystem partners, QNX offers a variety of solutions to support the robotics and industrial automation sector. This includes support for CANOpen, Time Sensitive Networking (TSN), Profinet, EtherCAT, Data Distribution Service (DDS), Message Queuing Telemetry Transport (MQTT), Modbus, and OPC Unified Architecture (OPC UA). For more details, contact us today.
What types of robots does QNX support?
For more than 40 years, QNX’s relentless dedication to technology advancements and real-world applications has been empowering the capabilities of the robotics industry. Our presence can be found in the following examples:
- Autonomous mobile robots (e.g. surface vehicles, underwater and aerial drones, warehouses, etc.)
- Automated guided vehicles
- Delta, articulated, SCARA, and cartesian robot manipulators for collaborative and industrial applications
- Surgical robots
- Autonomous robotic cleaners